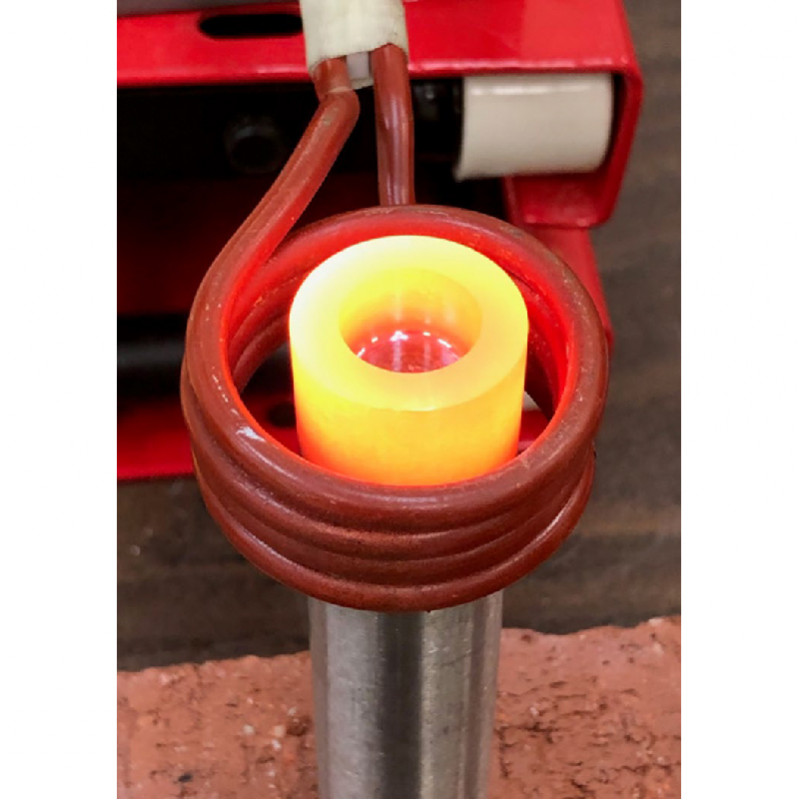
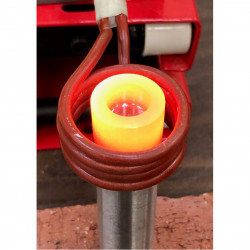
Морате бити пријављени да
Category
Фотографије су само у информативне сврхе. Погледајте спецификацију производа
please use latin characters
Objective: To heat a steel part for a brazing application; the client is manufacturing steel cable for the aerospace industry.
Frequency: 204 kHz
Material: Steel parts
Temperature: 1400 °F (760 °C)
A custom-designed multiple-turn helical coil was built to generate the required heating for the application. Temperature indicating paint was then applied to the part, which dissolves when the part reaches temperature. It took about 50 seconds to heat the part to temperature. The client was updating their induction system and this meets their time objectives.
Да ли вас занима овај производ? Да ли су вам потребне додатне информације или појединачне цене?
морате бити пријављени
Objective: To heat a steel part for a brazing application; the client is manufacturing steel cable for the aerospace industry.
Frequency: 204 kHz
Material: Steel parts
Temperature: 1400 °F (760 °C)
A custom-designed multiple-turn helical coil was built to generate the required heating for the application. Temperature indicating paint was then applied to the part, which dissolves when the part reaches temperature. It took about 50 seconds to heat the part to temperature. The client was updating their induction system and this meets their time objectives.
Vaša zahvalnost na komentar ne može biti registrovana
Prijavite nepristojan komentar
Prija nepristojnog komentara registrovana
Vaša prijava nepristojnog komentara ne može biti registrovana
Napišite vaš komentar
Komentar poslat
Vaš komentar ne može biti registrovan