1.The work, also knowsn as the onductor, is the component in the induction heating system that defines how effective and how efficently the work place is heated. Work coils range in complexity from a simple helical (or solenoid) wound coil consisting of a number of turns of copper tube wound around a mandrel to a coil precision machined from solid copper and brazed together.
The work coil is used to transfer the energy from the induction heating power supply and workhead to the work piece by generating an alternating electromagnetic field. The electromagnetic field generates a current that flows in the work piece as a mirror image to the current flowing in the work coil. As the current flows through the resistivity of the work piece it generates the heat within the work piece from I²R losses.
A second heating principle, hysteretic heating is also in effect when the work piece is a magnetic material such as carbon steel. Energy is generated within the work piece by the alternating magnetic field changing the magnetic polarity within the work piece. Hysteretic heating occurs in the work piece only up to the Curie temperature (750° C for steel) when the material’s magnetic permeability decreases to 1.
|
 |
2. Work Coil Basics A current flowing in a conductor creates a magnetic field. An alternating current creates an alternating field which produces an alternating current in a second conductor (the work piece). The current in the work piece is proportional to the field strength.
The transformer effect where the amount of current induced in the work piece is proportional to the number of turns on the coil and is generated as a mirror image of the work coil.
|
3. Coil Design Coil design is essential to the effectiveness and efficiency of an induction heating process. Ambrell designs the coil by first understanding where the heat needs to be generated in the part to perform the process, and then designs the coil to achieve the heating effect.
Induction coils are water-cooled copper conductors made of copper tubing that is readily formed into the shape of the coil for the induction heating process. Induction heating coils are cold and do not themselves get hot when water is flowing through them.
Matching the coil to the induction power supply is also essential to the efficiency of the process. Ambrell’s frequencyagile induction systems are easily matched to a wide range of coils by using the multi-tap output transformer in the power supply.
|
4. Experience and Excellence. Ambrell has installed over 10,000 systems across the world.
A hallmark of the Ambrell experience is complimentary laboratory testing. Ambrell’s Applications Engineers will test your parts, determine the correct system based on your requirements and also determine the optimal coil design. Ambrell’s in-house fabrication shop manufactures induction coils to ensure you receive the perfect coil for your application.
|
5. Multi-turn Helical Coil The helical (solenoid) is the most common and efficient coil with the number of turns defining the width of the heating pattern. The work piece can be stationary in the coil to provide a defined heating band in “single shot heating.” Or, the work piece is moved through the coil to heat the whole part with a highly uniform heating pattern called “scan heating.”
|
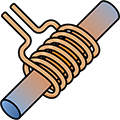 |
6. Single-Turn Coil.. Single-turn coils are ideal for heating a narrow band of a work piece or the tip of a work piece. These coils can also scan the length of a work piece and are commonly used for heat treating. These coils are often tight to the part to provide a precise heat pattern.
|
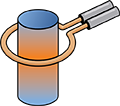 |
7. Multi-Position Helical Coil Multi-position coils are often used to produce more parts in a given time while allowing for the full heating process. While one work piece is being heated on one position, the other coil can be unloaded and reloaded for the next heating cycle. Any number of positions are possible but typically up to 8 positions are practical.
|
 |
8. Channel Coil Coils can be formed so the work piece is moved through the electromagnetic field by a linear transport mechanism. The work piece is heated as it moves through the channel coil and the coil can be configured to heat all of the part or just a single band.
|
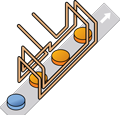 |
9. Curved Channel Coil Channel coils are often curved to fit onto a rotary table and are configured to occupy one of the steps in a multistep assembly process.
|
 |
10. Pancake Coil Pancake coils are used when it is necessary to heat the work piece from only one side or when its is not possible to surround the part.
|
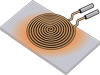 |
11. Concentrator Plate Coil Concentrator plates are used in single or multiple turn coils to focus the coil current to produce a defined heating effect in the work piece. These coils may also have a master coil with inserts designed to heat different shaped parts.
|
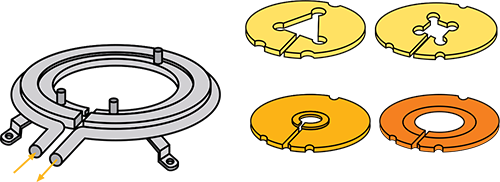 |
12. Coils and Conveyors Many parts are heated while being transported by a conveyor system. As long as the conveyor material is not electrically conductive, the magnetic field will pass through the conveyor and heat the work piece as it passes through the field.
|
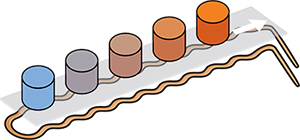 |
13. Hair-Pin Coil A long thin single- or multiple-turn coil is used to heat a long thin zone on a part, or used to heat a moving web of thin steel or aluminum.
|
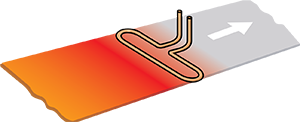 |
14. Split Helical Coil Single or multiple turn split helical coils are used when it’s not possible to get access to the heat area using a helical coil.
|
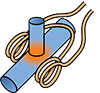 |
15. Internal Coil Internal bores can be heated using single- or multiple-turn
|
 |
16. EASYCOIL The flexible EASYCOIL is a coil that is ideal for large, irregularly shaped work pieces that cannot be heated with a traditional copper coil. It is used with Ambrell EASYHEAT™ and EKOHEAT® induction heating systems – up to the 250 kW model.
|
17. Wzbudniki w obudowie. Once the coil is designed, and heating pattern proven, it’s common to encapsulate the coil for thermal insulation from the process and to make the coil assembly more robust in harsh environments. Typical encapsulation materials are concrete, ceramics, and epoxy or thermoplastics.
Single-turn coil with ferrite concentrator. Field concentrators are used on coils to intensify the electromagnetic field, increasing the current density in the work piece. Concentrator materials are ferrites at high frequency and shim steel at low frequencies.
Multi-turn helical coil with turns fixed with studs and plates, also showing quick release connection blocks.
|