Морате бити пријављени да
-
moreX
-
Компоненте
-
-
Category
-
Полупроводници
- диоде
- Тиристори
-
Електро изоловани модули
- Електро изоловани модули | ВИСХАИ (ИР)
- Електро изоловани модули | ИНФИНЕОН (ЕУПЕЦ)
- Електро изоловани модули | Семикрон
- Електро изоловани модули | ПОВЕРЕКС
- Електро изоловани модули | ИКСИС
- Електро изоловани модули | ПОСЕИЦО
- Електро изоловани модули | АББ
- Електро изоловани модули | ТЕЦХСЕМ
- Go to the subcategory
- Мостовни исправљачи
-
Транзистори
- Транзистори | GeneSiC
- SiC MOSFET модули | Mitsubishi
- SiC MOSFET модули | STARPOWER
- АББ СиЦ МОСФЕТ модули
- IGBT модули | MITSUBISHI
- Транзисторски модули | MITSUBISHI
- MOSFET модули | MITSUBISHI
- Транзисторски модули | ABB
- ИГБТ модули | POWEREX
- ИГБТ модули | ИНФИНЕОН (ЕУПЕЦ)
- Silicijum-karbidni poluprovodnički elementi
- Go to the subcategory
- Гате Дриверс
- Блокови напајања
- Go to the subcategory
- Električni pretvarači
-
Пасивне компоненте (кондензатори, отпорници, осигурачи, филтери)
- Otpornici
-
Osigurači
- Minijaturni osigurači za elektronske sisteme serije ABC i AGC
- Cilindrični brzi osigurači
- Osigurači sa odloženim delovanjem GL/GG i AM karakteristika
- Ultra-brzi osigurači
- Brzi osigurači sa britanskim i američkim standardom
- Brzi osigurači sa evropskim standardom
- Vučni osigurači
- Visokonaponski osigurači
- Go to the subcategory
-
Kondenzatori
- Motorni kondenzatori
- Elektrolitski kondenzatori
- Kondenzatori - snubberi
- Energetski kondenzatori
- Kondenzatori za DC kola
- kondenzatori za kompenzaciju snage
- Visokonaponski kondenzatori
- Kondenzatori za indukciono grejanje
- Impulsni kondenzatori
- ДЦ ЛИНК кондензатори
- Кондензатори за АЦ/ДЦ кола
- Go to the subcategory
- EMI filtri
- Superkondenzatori
- Заштита од пренапона
- TEMPEST филтери за откривање емисије
- Go to the subcategory
-
Releji i kontaktori
- Теорија релеја и склопника
- Trofazni poluprovodnički releji
- Трофазни полупроводнички релеји наизменичне струје
- Регулатори, команде и додаци
- Sistemi za meki sart i reverziblni kontaktori
- Elektromehanički releji
- Kontaktori
- Rotacioni prekidači
-
Једнофазни полупроводнички релеји наизменичне струје
- Једнофазни релеји наизменичне струје, 1 серија | Д2425 | Д2450
- Jednofazni poluvodički izmjenični releji CWA i CWD serije
- Jednofazni poluvodički izmjenični releji CMRA i CMRD serije
- Jednofazni poluvodički izmjenični releji - serija PS
- Двоструки и четвороструки полупроводнички релеји наизменичне струје, серије Д24 Д, ТД24 К, Х12Д48 Д.
- Jednofazni poluvodički releji - gn serije
- Jednofazni kružni releji Ckr serije
- Jednofazni AC poluvodički releji za DIN sabirnice - ERDA I ERAA serija
- 150A AC jednofazni releji
- Čvrsti releji s ugrađenim hladnjakom na šini - ENDA, ERDA1 / ERAA1 series
- Go to the subcategory
- Monofazni poluprovodnički releji za štampane ploče
- Интерфејс релеји
- Go to the subcategory
- Indukcione komponenete
- Radijatori, Varistori, Termička zaštita
- Ventilatori
- Klimatizacija, Pribor za industrijska kućišta, Kuleri
-
Батерије, пуњачи, бафер напајања и претварачи
- Батерије, пуњачи - теоријски опис
- Litijum-jonske baterije. Nestandardne baterije. Sistem za upravljanje baterijom (BMS)
- Baterije
- Punjači i dodaci za baterije
- UPS i puferski izvori napajanja
- Pretvarači i dodaci- fotonaponski
- Складиште енергије
- Гориве ћелије
- Литијум-јонске батерије
- Go to the subcategory
- Automatika
-
Kablovi, Licnaste žice, Kablovski kanali, Fleksibilne veze
- жице
- лицнастим жице
- Каблови за специјалне намене
- схиртс
-
плетенице
- браидс флат
- плетенице коло
- Врло флексибилан плетеница - стан
- Врло флексибилан плетеница - коло
- Бакар плетена цилиндрични
- Бакра плетеница штит и цилиндрични
- Флексибилни уземљење траке
- Плетенице ЦИЛИНДРИЦАЛ поцинковани и нерђајућег челика
- ПВЦ изолацијом бакарне плетенице - Температура 85 ° Ц
- Стан плетени алуминијум
- Цоннецтион Кит - плетенице и цеви
- Go to the subcategory
- Прибор за вучу
- папучица
- Флексибилни исолатед сабирнице
- Вишеслојна флексибилан шина
- системи за управљање кабл
- Go to the subcategory
- View all categories
-
Полупроводници
-
-
- Suppliers
-
Applications
- Automatika industrijska
- CNC alatni strojevi
- DC i izmjenični pogoni (pretvarači)
- Energy bank
- Indukciono grejanje
- Industrijski zaštitni uređaji
- Istraživanje i laboratorijska merenja
- Mašine za sušenje i obradu drveta
- Mašine za termoformiranje
- Merenje i regulacija temperature
- Motori i transformatori
- Oprema i dijelovi za opasna područja (EX)
- Oprema za centrale, kontrolne ormare i telekomunikacije
- Poligrafija
- Rudarstvo, metalurgija i livnica
- Tramvajska i železnička vuča
- UPS i ispravljački sistemi
- Апарати за заваривање и апарати за заваривање
- Индустријска аутоматизација
- ХВАЦ аутоматизација
-
Инсталација
-
-
Индуктори
-
-
Индукциони уређаји
-
-
Услуга
-
- Kontakt
- Zobacz wszystkie kategorie
Industrial automatic and control systems
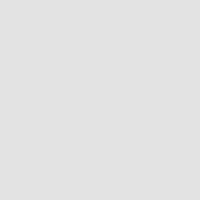
Industrial automation is currently one of the most quickly developing industrial sectors and has become an inseparable part of production processes - makes the company’s development process faster, improves systems, increases productivity, preciseness, and decreases production costs.
Automation is mostly used for controlling devices, systems and technological processes through various types of components e.g. drivers, controllers or control systems such as industrial computers and robots and their programming. Such systems are based on the operation of machines to replace manual work of people with automatics systems. Thanks to the feedback information they eliminate the need for operators and create highly independent systems, able to perform tasks without human assistance.
Industrial automation systems - why is it a good investment?
1. More precise information - limiting the need for performing periodical and manual inspections - automatic data collecting and support in choosing the best decisions.
2. Increase in productivity - lack of need for stopping the system during absence of workers/maintenance works - possibility of work 24h and 356 days a year.
3. Lower costs of:
- production,
- healthcare,
4. Increasing precision and quality of the products - limiting human errors; full efficiency of the factory thanks to the, unlike people, machines that do not experience fatigue.
5. More flexibility - simply programming the machine for a new task.
6. More safety - using machines in dangerous, extreme and risky conditions for people.
Disadvantages:
High initial costs while replacing manual production to the automatic production line. Additionally, this change can also require expenses for training of workers on how to use new equipment.
Automation devices and where to apply them
Industrial automation is mainly about controlling devices and technological processes and to achieve that it requires special components and their programming. We distinguish devices such as:
Programmable PLC drivers/controllers, which main task is to control devices and processes. They are usually used for simple controlling e.g. in small and uncomplicated systems in automation. Their functions include making commands to devices according to the indications from sensors, sharing data to operation panels or taking care of the input and output. In PLC drivers we distinguish e.g. module controllers - especially flexible and possible to be expanded or adjusted without the need to replace the main unit and other modules. In automation frequently used are also compact programmable controllers - used mainly in centralized systems.
Industrial computers - mostly used when PLC controllers are not enough. This type of computers, due to the highly effective components and numerous extension cards, allow to control much more complicated processes.
PAC controllers (Programmable Application Controller) - more complex equivalent of PLC controller with characteristics of an industrial computer. Widely used in complicated processes, requiring speed and possibility to handle significant amounts of data, e.g. in data acquisition or tasks connected to visualization.
Application of industrial automation
Automation systems predominantly handling supervision and visualization of processes (through e.g. WLAN) are composed i.e. industrial PC computers, computers for installing in the display, HMI systems and WLAN.
Another task of this type of systems is control - performed by using PLC drivers, HMI systems, field bus (CAN, EtherCAT, Profibus, etc.), WLAN and protection (SIL).
They also handle data processing and communication with the main PLC controller, which is provided by end devices such as launching devices, microcontrollers, engine controllers, industrial sensors, drive controllers, relays, switches, devices for direct control.
Why should you invest in automation systems?
Industrial automation control systems in recent years are getting a more and more necessary element of every workshop aiming for faster development, flexibility and improving service quality.
Control systems include integration of devices, machines and equipment, but also connect it with the rest of the company - handling e.g. supply chain, compliance processes, sales, and R&D. Automation and control systems, or IACS, can be controlled remotely, which can be both beneficial and risky, depending on the type of the company and their operation sector.
Types of control systems:
PLC control systems - a modern system based on PLC controllers, providing control over particular machines or technological lines.
SCADA - systems controlling technological/production processes and gathering process data. They handle collection of information, visualization of processes and informing about errors.
DCS - systems of scattered control - handle control and visualization of technological processes.
We also distinguish:
Enterprise Resource Planning (ERP) - support e.g. accounting and distribution.
Manufacturing Execution System (MES) - production realization systems, supporting data collection and optimization of production processes in the business area.
Basic Process Control System (BPCS) - process control systems, monitoring the workshop, basing on information from sensors and process instruments.
Safety instrumented system (SIS) - is composed of a set of programs and hardware and software control systems - especially used in refineries, chemical and nuclear facilities.
Related products
Related posts
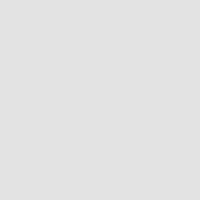
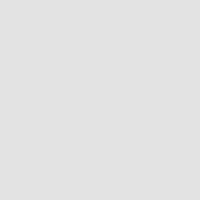
Leave a comment