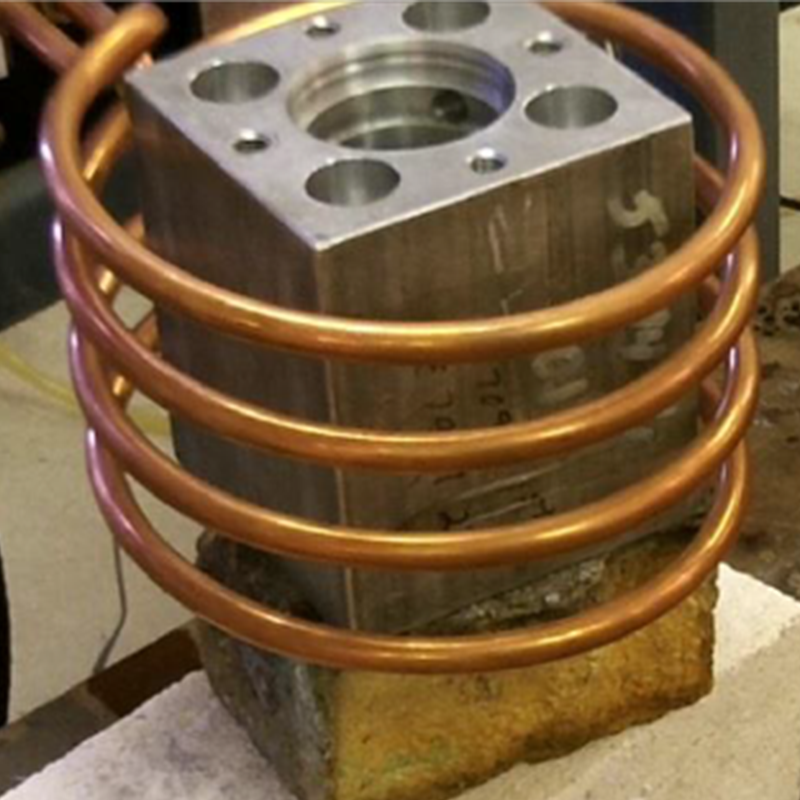
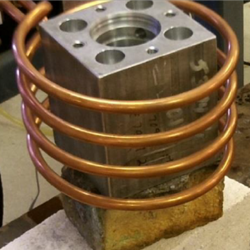
trebuie să fii logat
Category
Fotografiile au doar scop informativ. Vizualizați specificațiile produsului
please use latin characters
Objective: To heat an aluminum block for a cylinder liner coating curing application.
Equipment:
Frequency: 89 kHz
Material: Aluminum block - 4" x 4" x 4.5" (102 x 102 x 114 mm)
Temperature: 400 °F (204 °C)
Testing: The aluminum part was placed inside the helical coil with temperature indicating paint applied to both the inside and outside of the block. The power was turned on and the part began to heat. After 90 seconds the temperature indicating paint began to melt.
Benefits:
Sunteți interesat de acest produs? Aveți nevoie de informații suplimentare sau de prețuri individuale?
trebuie să fii logat
Objective: To heat an aluminum block for a cylinder liner coating curing application.
Equipment:
Frequency: 89 kHz
Material: Aluminum block - 4" x 4" x 4.5" (102 x 102 x 114 mm)
Temperature: 400 °F (204 °C)
Testing: The aluminum part was placed inside the helical coil with temperature indicating paint applied to both the inside and outside of the block. The power was turned on and the part began to heat. After 90 seconds the temperature indicating paint began to melt.
Benefits:
Aprecierea ta pentru recenzie nu a putut fi trimisa
Reclama un comentariu
Raport trimis
Reclamatia tau nu a putut fi trimisa
Scrie-ti recenzia
Recenzia a fost trimisa
Recenzia ta nu a putut fi trimisa