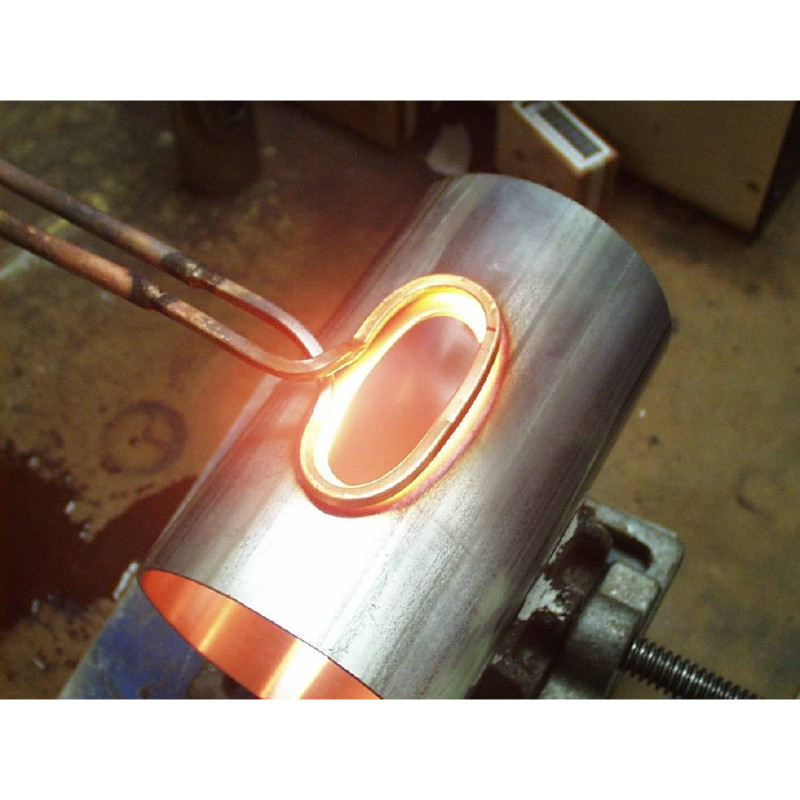
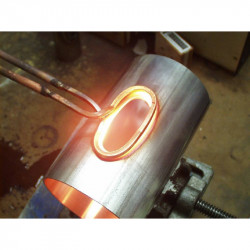
Debes estar logueado
Category
Las fotos son solo para fines informativos. Ver especificaciones de producto
please use latin characters
Objective: To anneal a ¼” area around an oval cutout on a stainless steel tube prior to extrusion.
Frequency: 300 kHz
Material: .75” (19mm), 1.5” (38.1mm) and 4” (101.6mm) diameter steel tubes
Temperature: 1900 °F (1038 °C)
A single turn helical coil is used on the 4” (101.6mm) diameter tubes and a two turn helical coil is used on the smaller diameters. The coil is placed over the oval cutout and power is supplied for 15 seconds to anneal a 0.25" (6.35mm) diameter around the cutout.
¿Estás interesado en este producto? ¿Necesita información adicional o precios individuales?
Usted debe estar conectado
Objective: To anneal a ¼” area around an oval cutout on a stainless steel tube prior to extrusion.
Frequency: 300 kHz
Material: .75” (19mm), 1.5” (38.1mm) and 4” (101.6mm) diameter steel tubes
Temperature: 1900 °F (1038 °C)
A single turn helical coil is used on the 4” (101.6mm) diameter tubes and a two turn helical coil is used on the smaller diameters. The coil is placed over the oval cutout and power is supplied for 15 seconds to anneal a 0.25" (6.35mm) diameter around the cutout.
Su agradecimiento a la reseña no pudo ser enviado
Reportar comentario
Reporte enviado
Su reporte no pudo ser enviado
Escriba su propia reseña
Reseña enviada
Su reseña no pudo ser enviada