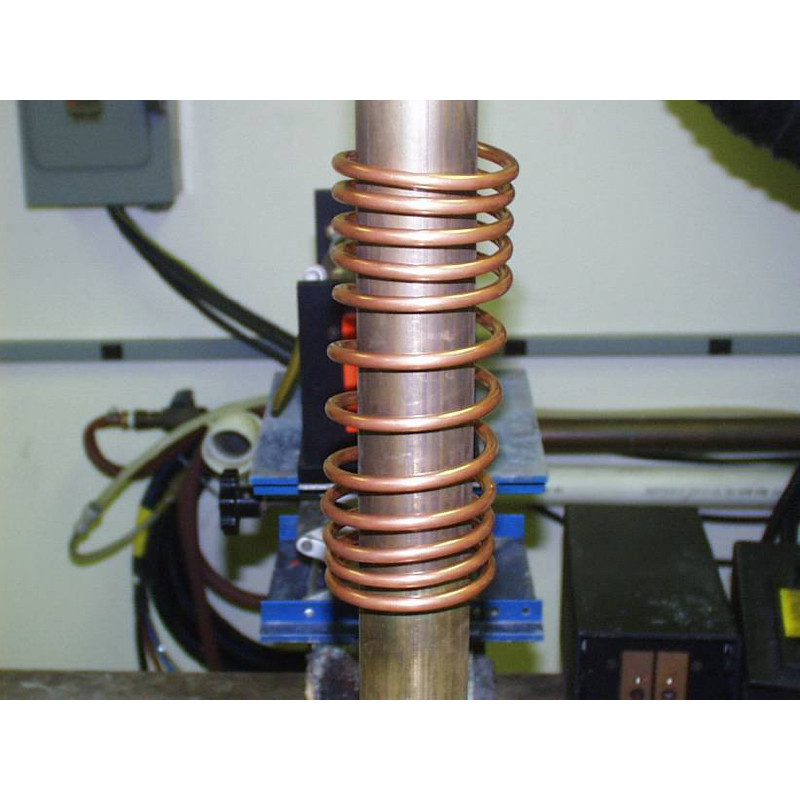
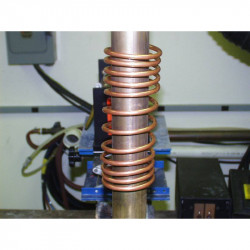
Debes estar logueado
Category
Las fotos son solo para fines informativos. Ver especificaciones de producto
please use latin characters
Objective: Annealing brass and bronze tubing for bending in a mandrel bender to form handrails.
Frequency: 228 kHz
Temperature: 1000 °F (538 °C)
A twelve turn helical coil is used to heat an 8” (20.3cm) area 3” (7.6cm) above the end of the tube. Each of the four tubes require a different heat cycle and time to reach the required temperature. Please see the chart below for each tube.
1.5" | 1.5" | 2" | 2" | |
Brass | Bronze | Brass | Bronze | |
Heat Cycle Time [s] | 80 | 100 | 100 | 120 |
Power [kW] | 4 | 4.15 | 3.1 | 3.4 |
Current [A] | 248 | 255 | 200 | 212 |
Frequency [kHz] | 197 | 197 | 228 | 228 |
¿Estás interesado en este producto? ¿Necesita información adicional o precios individuales?
Usted debe estar conectado
Objective: Annealing brass and bronze tubing for bending in a mandrel bender to form handrails.
Frequency: 228 kHz
Temperature: 1000 °F (538 °C)
A twelve turn helical coil is used to heat an 8” (20.3cm) area 3” (7.6cm) above the end of the tube. Each of the four tubes require a different heat cycle and time to reach the required temperature. Please see the chart below for each tube.
1.5" | 1.5" | 2" | 2" | |
Brass | Bronze | Brass | Bronze | |
Heat Cycle Time [s] | 80 | 100 | 100 | 120 |
Power [kW] | 4 | 4.15 | 3.1 | 3.4 |
Current [A] | 248 | 255 | 200 | 212 |
Frequency [kHz] | 197 | 197 | 228 | 228 |
Su agradecimiento a la reseña no pudo ser enviado
Reportar comentario
Reporte enviado
Su reporte no pudo ser enviado
Escriba su propia reseña
Reseña enviada
Su reseña no pudo ser enviada