Musisz być zalogowany/a
-
WróćX
-
Podzespoły
-
-
Category
-
Półprzewodniki
- Diody
-
Tyrystory
- Tyrystory firmy VISHAY (IR)
- Tyrystory firmy LAMINA
- Tyrystory firmy INFINEON (EUPEC)
- Tyrystory firmy ESTEL
- Tyrystory firmy WESTCODE
- Tyrystory firmy Semikron
- Tyrystory firmy POWEREX
- Tyrystory firmy DYNEX
- Tyrystory do grzejnictwa indukcyjnego
- Tyrystory firmy ABB
- Tyrystory firmy TECHSEM
- Przejdź do podkategorii
-
Moduły elektroizolowane
- Moduły elektroizolowane firmy VISHAY (IR)
- Moduły elektroizolowane firmy INFINEON (EUPEC)
- Moduły elektroizolowane firmy Semikron
- Moduły elektroizolowane firmy POWEREX
- Moduły elektroizolowane firmy IXYS
- Moduły elektroizolowane firmy POSEICO
- Moduły elektroizolowane firmy ABB
- Moduły elektroizolowane firmy TECHSEM
- Przejdź do podkategorii
- Mostki prostownicze
-
Tranzystory
- Tranzystory firmy GeneSiC
- Moduły SiC MOSFET firmy Mitsubishi
- Moduły SiC MOSFET firmy STARPOWER
- Moduły SiC MOSFET firmy ABB
- Moduły IGBT firmy MITSUBISHI
- Moduły tranzystorowe firmy MITSUBISHI
- Moduły MOSFET firmy MITSUBISHI
- Moduły tranzystorowe firmy ABB
- Moduły IGBT firmy POWEREX
- Moduły IGBT - firmy INFINEON (EUPEC)
- Elementy półprzewodnikowe z węglika krzemu
- Przejdź do podkategorii
- Sterowniki
- Bloki mocy
- Przejdź do podkategorii
- Przetworniki prądowe i napięciowe LEM
-
Elementy pasywne (kondensatory, rezystory, bezpieczniki, filtry)
- Rezystory
-
Bezpieczniki
- Bezpieczniki miniaturowe do układów elektronicznych seria ABC i AGC
- Bezpieczniki szybkie rurkowe
- Wkładki zwłoczne o charakterystykach GL/GG oraz AM
- Wkładki topikowe ultraszybkie
- Bezpieczniki szybkie standard brytyjski i amerykański
- Bezpieczniki szybkie standard europejski
- Bezpieczniki trakcyjne
- Wkładki bezpiecznikowe wysokonapięciowe
- Przejdź do podkategorii
-
Kondensatory
- Kondensatory do silników
- Kondensatory elektrolityczne
- Kondensatory foliowe Icel
- Kondensatory mocy
- Kondensatory do obwodów DC
- Kondensatory do kompensacji mocy
- Kondensatory wysokonapięciowe
- Kondensatory do grzejnictwa indukcyjnego
- Kondensatory impulsowe
- Kondensatory DC LINK
- Kondensatory do obwodów AC/DC
- Przejdź do podkategorii
- Filtry przeciwzakłóceniowe
- Superkondensatory
-
Zabezpieczenia przeciwprzepięciowe
- Ograniczniki przepięć dla aplikacji RF
- Ograniczniki przepięć dla systemów wizyjnych
- Ograniczniki przepięć linii zasilających
- Ograniczniki przepięć do LED
- Ograniczniki przepięć do Fotowoltaiki
- Ograniczniki przepięć dla systemów wagowych
- Ograniczniki przepięć dla magistrali Fieldbus
- Przejdź do podkategorii
- Filtry emisji ujawniającej TEMPEST
- Przejdź do podkategorii
-
Przekaźniki i Styczniki
- Teoria przekaźniki i styczniki
- Przekaźniki półprzewodnikowe AC 3-fazowe
- Przekaźniki półprzewodnikowe DC
- Regulatory, układy sterujące i akcesoria
- Soft starty i styczniki nawrotne
- Przekaźniki elektromechaniczne
- Styczniki
- Przełączniki obrotowe
-
Przekaźniki półprzewodnikowe AC 1-fazowe
- Przekaźniki półprzewodnikowe AC jednofazowe serii 1 | D2425 | D2450
- Przekaźniki półprzewodnikowe AC jednofazowe serii CWA I CWD
- Przekażniki półprzewodnikowe AC jednofazowe serii CMRA I CMRD
- Przekaźniki półprzewodnikowe AC jednofazowe serii PS
- Przekaźniki półprzewodnikowe AC podwójne i poczwórne serii D24 D, TD24 Q, H12D48 D
- 1-fazowe przekaźniki półprzewodnikowe serii gn
- Przekaźniki półprzewodnikowe ac jednofazowe serii ckr
- Przekaźniki AC jednofazowe na szynę din SERII ERDA I ERAA
- Przekaźniki jednofazowe AC na prąd 150A
- Podwójne przekaźniki półprzewodnikowe zintegrowane z radiatorem na szynę DIN
- Przejdź do podkategorii
- Przekaźniki półprzewodnikowe AC 1-fazowe do druku
- Przekaźniki interfejsowe
- Przejdź do podkategorii
- Rdzenie oraz inne elementy indukcyjne
- Radiatory, Warystory, Zabezpieczenia termiczne
- Wentylatory
- Klimatyzacja, Osprzęt do szaf rozdzielczych, Chłodnice
-
Akumulatory, ładowarki, zasilacze buforowe i przetwornice
- Akumulatory, ładowarki - opis teoretyczny
- Baterie litowo-jonowe. Niestandardowe baterie. System zarządzania baterią (BMS)
- Akumulatory
- Ładowarki akumulatorów i akcesoria
- Zasilacze UPS i zasilacze buforowe
- Przetwornice i osprzęt do fotowoltaiki
- Magazyny energii
- Wodorowe ogniwa paliwowe
- Ogniwa litowo-jonowe
- Przejdź do podkategorii
-
Automatyka
- Podnośniki Spiralift
- Części do dronów Futaba
- Wyłączniki krańcowe, Mikrowyłączniki
- Czujniki, Przetworniki
- Pirometry
- Liczniki, Przekaźniki czasowe, Mierniki tablicowe
- Przemysłowe urządzenia ochronne
- Sygnalizacja świetlna i dźwiękowa
- Kamera termowizyjna
- Wyświetlacze LED
- Przyciski i przełączniki
- Przejdź do podkategorii
-
Przewody, Lica, Peszle, Połączenia elastyczne
- Druty
- Przepusty kablowe i mufy
- Lica
-
Kable do zastosowań specjalnych
- Przewody przedłużające i kompensujące
- Przewody do termopar
- Przewody podłączeniowe do czyjnków PT
- Przewody wielożyłowe temp. -60°C do +1400°C
- SILICOUL przewody średniego napięcia
- Przewody zapłonowe
- Przewody grzejne
- Przewody jednożyłowe temp. -60°C do +450°C
- Przewody kolejowe
- Przewody grzejne w Ex
- Przewody dla przemysłu obronnego
- Przejdź do podkategorii
- Koszulki
-
Plecionki
- Plecionki płaskie
- Plecionki okrągłe
- Bardzo giętkie plecionki - płaskie
- Bardzo giętkie plecionki - okrągłe
- Miedziane plecionki cylindryczne
- Miedziane plecionki cylindryczne i osłony
- Paski uziemiające giętkie
- Plecionki cylindryczne z ocynkowanej i nierdzewnej stali
- Miedziane plecionki izolowane PCV - temperatura do 85 stopni C
- Płaskie plecionki aluminiowe
- Zestaw połączeniowy - plecionki i rurki
- Przejdź do podkategorii
- Osprzęt dla trakcji
- Końcówki kablowe
- Szyny elastyczne izolowane
- Wielowarstwowe szyny elastyczne
- Systemy prowadzenia kabli
- Przejdź do podkategorii
- Zobacz wszystkie kategorie
-
Półprzewodniki
-
-
- Dostawcy
-
Aplikacje
- Automatyka HVAC
- Automatyka przemysłowa
- Banki energii
- Energetyka
- Górnictwo, hutnictwo i odlewnictwo
- Maszyny do suszenia i obróbki drewna
- Maszyny do termo-formowania tworzyw sztucznych
- Nagrzewanie indukcyjne
- Napędy prądu stałego i przemiennego (falowniki)
- Obrabiarki CNC
- Podzespoły do stref zagrożonych wybuchem (EX)
- Poligrafia
- Pomiar i regulacja temperatury
- Pomiary badawcze i laboratoryjne
- Przemysłowe urządzenia ochronne
- Silniki i transformatory
- Spawarki i zgrzewarki
- Trakcja tramwajowa i kolejowa
- Wyposażenie do szaf rozdzielczych i sterowniczych
- Zasilacze (UPS) i układy prostownikowe
-
Montaż
-
-
Induktory
-
-
Urządzenia indukcyjne
-
-
Serwis i naprawy
-
- Kontakt
- Zobacz wszystkie kategorie
Monitorowanie stanu technicznego maszyn przemysłowych
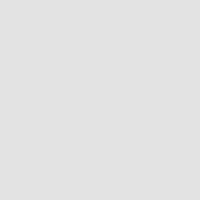
Przed zakładami posiadającymi linie produkcyjne stoi wiele wyzwań. Czwartą już z kolei rewolucją przemysłową będzie automatyzacja procesów produkcyjnych. Monitorowanie Stanu technicznego maszyn to podstawa do skutecznego podejmowania lepszych decyzji wpływających bezpośrednio na proces produkcji, jego organizację i całą linię produkcyjną. Monitorowanie maszyn to podstawowy element produkcji wykorzystującej dane, która wpisuje się idealnie w założenia rewolucji przemysłowej 4.0.
Na czym polega monitorowanie maszyn?
Maszyny monitorujemy przede wszystkim, aby uniknąć ich awarii. Kompleksowa i stała obserwacja zmniejsza prawdopodobieństwo wystąpienia przestojów produkcyjnych, które niezaprzeczalnie mają negatywny wpływ na proces produkcyjny. Każdy przestój wiąże się ze stratami finansowymi, zatrzymaniem produkcji i niezadowolonymi klientami. W celu uniknięcia przestojów monitoruje się maszyny i przeprowadza szeroko zakrojoną diagnostykę linii produkcyjnych.
Definicja diagnostyki
Diagnostyka to określanie stanu technicznego urządzeń i ustalanie źródeł awarii. Najprostszą i najbardziej znaną metodą diagnozowania maszyn są okresowe pomiary poziomów drgań. Pomiar taki wykonać można aparaturą diagnostyczną taką jak: prostymi i przenośnymi miernikami, przenośnymi analizatorami sygnału lub aparaturą stacjonarną do monitorowania, ale mogą to być również systemy on-line.
Wspólnym elementem w każdej technologii i każdym rozwiązaniu jest wykorzystywanie danych. Dane pomagają nam w sposób bardzo dokładny określić aktualny stan maszyny i jej wydajność, a także mogą wychwycić przyszłe awarie i pozwolić na odpowiednie zaplanowanie harmonogramu konserwacji, tak aby przestój był możliwie jak najbardziej krótki. Wszystko to sprawia, że zdalna możliwość monitorowania stanu maszyn staje się podstawą w funkcjonowaniu każdego zakładu.
Diagnostyka planowo-zapobiegawcza
Słowem-kluczem w diagnostyce planowo-zapobiegawczej jest harmonogram. Skuteczny harmonogram konserwacji, remontów i obsługi technicznej to podstawa działania każdej dobrze działającej linii produkcyjnej. Maszyny i urządzenia zużywają się, a im częściej są konserwowane tym zmniejsza się prawdopodobieństwo wystąpienia nieplanowanego przestoju. Podstawą do planowania przyszłych ruchów związanych z konserwacją jest analiza danych historycznych oraz przeprowadzenie analizy. W zależności od grupy krytyczności, do której należą maszyny dobierana jest strategia eksploatacji maszyn. Dla przykładu przeglądy i naprawy nie muszą być zaplanowane, a decyzja o nich może być podejmowana dynamicznie, w oparciu o aktualny stan techniczny, w którym znajdują się maszyny.
Druga strategia to tzw. predykcja w utrzymaniu ruchu, czyli optymalne użytkowanie urządzeń. Predykcja to planowanie i wyznaczanie konkretnych terminów przeglądów i konserwacji poprzez określanie stanu urządzeń, w którym znajdą się w przyszłości.
Sygnały diagnostyczne
Do przenoszenia sygnałów diagnostycznych służą układy bezpieczeństwa takie jak wieże sygnalizacyjne. W momencie pojawienia się ryzyka wystąpienia na przykład awarii systemu informują, ostrzegają lub alarmują o zdarzeniu. Ściśle połączony system wież optycznych i/lub dźwiękowych z czujnikami umieszczonymi na linii produkcyjnej to podstawa, aby szybko zareagować, uniknąć lub szybko naprawić awarię.
Sprawdź, również jak wygląda optymalizacja i diagnostyka linii produkcyjnych.
Powiązane posty
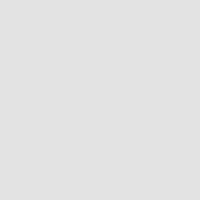
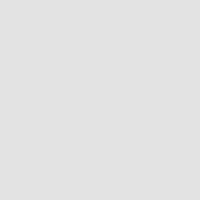
Dodaj komentarz