Musisz być zalogowany/a
Czym jest EMI i dlaczego warto się nim przejmować?
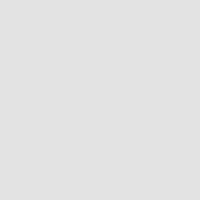
Współczesne urządzenia elektroniczne są coraz mniejsze, bardziej złożone i działają z coraz wyższymi częstotliwościami. Wszystko to sprawia, że stają się także bardziej wrażliwe na zakłócenia elektromagnetyczne (Electromagnetic Interference – EMI), czyli niechciane sygnały promieniowane lub przewodzone, które mogą wpływać na działanie układów elektronicznych własnych jak i sąsiadujących.
EMI może powodować szereg problemów — od drobnych zakłóceń w pracy urządzenia aż po całkowitą awarię systemu. Dlatego tak ważne jest, aby już na etapie projektu zadbać o jego odporność na zakłócenia oraz ograniczyć emisję zakłóceń do otoczenia.
Jednym z najskuteczniejszych sposobów radzenia sobie z tym problemem jest ekranowanie elektromagnetyczne. W tym artykule przyjrzymy się bliżej temu, jak działa ekranowanie EMI na poziomie płytki PCB, dlaczego jest ważne, jak dobrać odpowiednie materiały i jak zaprojektować skuteczne ekrany EMC. Zaczniemy od podstaw fal elektromagnetycznych, a potem przejdziemy przez konkretne techniki projektowe oraz najczęstsze pułapki.
Fale elektromagnetyczne i ich charakterystyka
Zanim zaczniemy projektować warto zrozumieć, z czym właściwie mamy do czynienia. Zakłócenia elektromagnetyczne to nic innego jak fale elektromagnetyczne, które mogą zakłócać pracę układów elektronicznych — czy to przez emisję z samego urządzenia, czy przez wpływ otoczenia.
Z czego składa się fala elektromagnetyczna?
Fala elektromagnetyczna (EM) składa się z dwóch powiązanych ze sobą pól:
- pola elektrycznego (E)
- pola magnetycznego (H)
Oba te pola są prostopadłe względem siebie i względem kierunku propagacji fali. Wyobraź sobie strzałkę lecącą w prawo: pole elektryczne będzie „w górę i w dół”, pole magnetyczne „na boki”, a fala porusza się do przodu.
To współdziałanie pól E i H sprawia, że fale EM mogą się przemieszczać w przestrzeni — także w kierunku Twojej płytki PCB, gdzie mogą powodować spore problemy.
Impedancja fali elektromagnetycznej (Z)
Każda fala EM charakteryzuje się tzw. impedancją fali, która określa stosunek natężenia pola elektrycznego do pola magnetycznego.
W przypadku powietrza lub próżni impedancja wynosi około 377 omów (Ω). To tzw. impedancja wolnej przestrzeni.
Znajomość tej wartości pozwala nam zrozumieć, jak fala będzie się zachowywać przy kontakcie z różnymi materiałami ekranującymi – co stanie się kluczowe w kolejnych rozdziałach.
Fale dominująco elektryczne vs. dominująco magnetyczne
W zależności od impedancji fali możemy wyróżnić dwa typy fal:
- Fale dominująco elektryczne – mają wysoką impedancję (większą niż 377 Ω). Typowo występują w sytuacjach otwartych przestrzeni lub przy długich przewodach sygnałowych.
- Fale dominująco magnetyczne – mają niską impedancję (poniżej 377 Ω). Zazwyczaj są generowane w bliskiej odległości od źródła, np. przy transformatorach, silnikach czy zasilaczach impulsowych.
Dlaczego to ważne? Bo różne typy fal oddziałują inaczej z materiałami ekranującymi. Dla fal o wysokiej impedancji ważna jest utrata odbicia. Dla tych o niskiej – utrata absorpcji. Inaczej mówiąc: nie każda tarcza EMC działa tak samo na każdy rodzaj zakłócenia.
Podstawy ekranowania EMI na poziomie PCB
Gdy już rozumiemy, czym są fale elektromagnetyczne i jak się rozchodzą, czas przejść do sposobów ich kontrolowania. Jednym z najbardziej skutecznych i popularnych rozwiązań jest ekranowanie EMI na poziomie płytki PCB. To podejście pozwala tłumić zakłócenia u źródła — zanim rozprzestrzenią się lub zakłócą inne elementy układu.
Czym jest obudowa ekranująca na poziomie płytki PCB?
Ekrany PCB to po prostu miniaturowa obudowa z metalu (często w formie puszki lub „nakładki”), która zakrywa określoną część układu elektronicznego na PCB. Technicznie to klatka Faradaya, której zadaniem jest:
- blokowanie fal elektromagnetycznych z zewnątrz, zanim dotrą do wrażliwych komponentów (np. układów analogowych),
- ograniczanie emisji zakłóceń z układu — czyli powstrzymywanie „szumów” przed opuszczeniem źródła.
W praktyce ekranowanie na poziomie PCB chroni zarówno Twoją elektronikę, jak i inne urządzenia wokół niej.
Dlaczego warto stosować ekranowanie na poziomie płytki PCB?
- Ochrona czułych obwodów – takich jak wzmacniacze, przetworniki analogowe, układy RF.
- Redukcja emisji EMC – kluczowe w spełnianiu norm (np. CE, FCC).
- Lokalne tłumienie zakłóceń – skuteczniejsze niż globalna obudowa przy źródłach wysokiej emisji.
W wielu przypadkach ekranowanie już na etapie PCB pozwala uniknąć bardziej kosztownych rozwiązań na poziomie całej obudowy — co oznacza mniejsze koszty i prostszy projekt.
Skuteczność ekranowania (Shielding Effectiveness – SE)
Aby ocenić, jak dobrze działa ekran, stosuje się parametr zwany skutecznością ekranowania (SE). Jest on wyrażony w decybelach (dB) i opisuje, o ile decybeli zmniejszono natężenie pola elektromagnetycznego dzięki zastosowaniu ekranu PCB.
SE=20log10(Ebez/Ez)
Gdzie:
- Ebez to natężenie pola przed ekranem,
- Ez to natężenie pola po zastosowaniu ekranu.
Przykład: SE = 40 dB oznacza, że ekran tłumi fale 100 razy (w sensie amplitudy) albo 10 000 razy pod względem mocy.
Co wpływa na SE?
Skuteczność ekranowania zależy od wielu czynników:
- materiału obudowy,
- grubości obudowy,
- rodzaju fali EM (elektryczna vs. magnetyczna),
- obecności otworów i nieszczelności,
- częstotliwości sygnału.
SE jest wartością złożoną — i właśnie dlatego kolejne rozdziały zagłębią się szczegółowo w mechanizmy działania ekranów i wybór materiału.
Mechanizmy działania obudów ekranowanych EMI
Aby efektywnie projektować ekranowanie EMC, nie wystarczy tylko znać poziom skuteczności w decybelach. Trzeba rozumieć, jak obudowy ekranujące EMI działają fizycznie – czyli jakie zjawiska zachodzą, gdy fala elektromagnetyczna napotyka przeszkodę. W grę wchodzą trzy podstawowe mechanizmy: odbicie, absorpcja oraz transmisja.
Odbicie – pierwszy poziom obrony
Gdy fala EM trafia na przewodzący materiał (np. miedź), znacząca część energii jest po prostu odbita. Dzieje się tak dlatego, że:
- pole elektryczne nie może penetrować wnętrza idealnego przewodnika (E = 0),
- pole magnetyczne wywołuje prądy wirowe (indukowane), które wytwarzają pole przeciwdziałające jego zmianom (reguła Lenza).
Z tego powodu:
- fale elektrycznie dominujące (wysoka impedancja) są skutecznie tłumione przez odbicie,
- ale fale magnetycznie dominujące (niska impedancja) łatwiej przenikają przez cienkie warstwy – dlatego tu sam efekt odbicia może nie wystarczyć.
Absorpcja – druga linia obrony
Część energii, która nie została odbita, wchodzi do wnętrza osłony. Wtedy pojawia się drugi mechanizm: absorpcja, czyli konwersja energii pola EM w ciepło. Zachodzi ona głównie dzięki:
- prądom wirowym (eddy currents),
- stratom dielektrycznym (jeśli materiał nie jest idealnym przewodnikiem).
Stopień absorpcji zależy od kilku czynników:
- materiału (np. stal lepiej pochłania pole magnetyczne niż miedź),
- grubości warstwy – w relacji do głębokości wnikania (skin depth),
- częstotliwości sygnału – im wyższa, tym mniejsza głębokość wnikania, a więc lepsza absorpcja cienkim ekranem.
Warto wiedzieć: Dla fali magnetycznej absorpcja ma większe znaczenie niż odbicie, zwłaszcza przy niskich częstotliwościach.
Transmisja – to, co „przecieka”
Niestety, żadna osłona nie jest doskonała. Część energii przechodzi dalej – to tzw. transmisja, czyli resztkowa fala, która przeszła przez barierę. Celem projektanta jest:
- zminimalizować transmisję poprzez odpowiedni dobór materiału i grubości,
- zredukować wszelkie nieszczelności, przez które może uciec energia EMI
Kiedy liczy się odbicie, a kiedy absorpcja?
To, który mechanizm ekranowania ma większe znaczenie – odbicie czy absorpcja – zależy od charakteru fali elektromagnetycznej, czyli od tego, czy dominuje w niej pole elektryczne, czy magnetyczne. Kluczowym parametrem, który to określa, jest impedancja fali elektromagnetycznej.
Jeśli fala ma wysoką impedancję, zbliżoną do 377 Ω (czyli tzw. impedancji próżni), oznacza to, że dominującym składnikiem jest pole elektryczne. W takim przypadku główną rolę w ekranowaniu odgrywa odbicie – ponieważ pole elektryczne bardzo łatwo odbija się od powierzchni dobrze przewodzących. Dlatego do tłumienia tego rodzaju fal najlepiej nadają się materiały o wysokiej przewodności, takie jak miedź czy aluminium.
Z kolei gdy fala ma niską impedancję (znacznie mniejszą niż 100 Ω), oznacza to, że przeważa w niej składnik magnetyczny. W takich przypadkach odbicie jest mniej skuteczne, ponieważ pole magnetyczne łatwiej przenika przez cienkie przewodniki. Tu z pomocą przychodzi drugi mechanizm – absorpcja, czyli pochłanianie energii fali wewnątrz materiału. Aby ten mechanizm działał skutecznie, potrzebne są materiały o wysokiej przenikalności magnetycznej, takie jak stal, żelazo, a w niektórych zastosowaniach nawet specjalne ferrytowe kompozyty.
W praktyce wiele rzeczywistych źródeł zakłóceń emituje fale o złożonym charakterze – ani czysto elektrycznym, ani czysto magnetycznym. Dlatego w większości aplikacji projektanci stosują podejście mieszane: łączy się mechanizmy odbicia i absorpcji, dobierając materiały tak, by ekranowanie było skuteczne w szerokim zakresie częstotliwości i typów zakłóceń.
Jeśli nie wiesz, z jaką falą masz do czynienia – załóż, że potrzebujesz obu mechanizmów. Dlatego w praktyce używa się często materiałów kompozytowych lub ekranów wielowarstwowych.
Wybór materiału ekranu EMI – porównania i rekomendacje
Dobór materiału do ekranowania EMI to nie tylko kwestia ceny i dostępności, ale przede wszystkim jego właściwości fizycznych – przewodności elektrycznej, przenikalności magnetycznej oraz grubości warstwy. Każdy materiał zachowuje się inaczej w zależności od częstotliwości zakłóceń i dominującego typu pola (elektrycznego lub magnetycznego), co ma bezpośredni wpływ na skuteczność ekranowania.
Miedź – złoty standard ekranowania
Miedź to najczęściej wybierany materiał do ekranowania EMI – i to nie bez powodu. Jej bardzo wysoka przewodność elektryczna sprawia, że doskonale odbija fale o wysokiej impedancji, czyli te, w których dominuje pole elektryczne. Dzięki temu świetnie sprawdza się w ekranowaniu obwodów radiowych, sygnałów wysokoczęstotliwościowych oraz ogólnych emisji z PCB. Miedź jest też stosunkowo łatwa w obróbce i dobrze przylega do powierzchni płytek drukowanych.
Warto pamiętać: miedź nie jest idealna do tłumienia silnych pól magnetycznych o niskiej częstotliwości – w takich przypadkach potrzebny jest materiał o większej przenikalności magnetycznej.
Stal – gdy dominują zakłócenia magnetyczne
Stal (a konkretnie – miękka stal o niskiej zawartości węgla) jest znakomita w tłumieniu pola magnetycznego, szczególnie w zakresie niskich częstotliwości. Dzieje się tak dzięki jej wysokiej przenikalności magnetycznej, która umożliwia absorpcję energii pola H wewnątrz materiału. W związku z tym stal świetnie sprawdza się jako ekran wokół transformatorów, silników, kabli zasilających czy innych źródeł zakłóceń magnetycznych.
Jej wadą jest większy ciężar i niższa przewodność elektryczna niż miedź, przez co mniej efektywnie odbija fale elektryczne – dlatego najczęściej stosuje się ją w połączeniu z innymi materiałami (np. stal niklowana lub stal pokryta miedzią).
Mosiądz – kompromisowy wybór
Mosiądz, jako stop miedzi i cynku, oferuje kompromis pomiędzy kosztami, przewodnością a właściwościami mechanicznymi. Ma nieco niższą przewodność niż czysta miedź, ale za to większą odporność na korozję i sztywność. Nadaje się do ogólnego ekranowania, zwłaszcza w aplikacjach mechanicznie wymagających – np. obudowach przemysłowych lub ekranach formowanych jako złożone kształty.
Projektowanie ekranowania EMC z uwzględnieniem szczelin i otworów
W praktycznych zastosowaniach obudowa rzadko ma postać idealnie jednolitej powierzchni. W rzeczywistych konstrukcjach PCB i ich obudowach zawsze występują szczeliny, przysłony, szwy technologiczne lub otwory wentylacyjne. Choć często są konieczne z powodów konstrukcyjnych, mogą one znacząco obniżyć skuteczność ekranowania.
Wpływ szczelin (szwów, otworów) na skuteczność ekranowania
Każda szczelina w ekranie stanowi potencjalne miejsce, przez które fale elektromagnetyczne mogą się przedostać – zarówno do wnętrza chronionej przestrzeni, jak i na zewnątrz. Skuteczność ekranowania w takich przypadkach spada, zwłaszcza w przypadku wyższych częstotliwości, gdzie nawet niewielkie szczeliny mogą działać jak anteny szczelinowe.
Szczeliny w ekranie mogą powodować:
- Wyciek fal – szczególnie przy wysokich częstotliwościach, gdzie długość fali jest porównywalna lub mniejsza od wymiarów otworu.
- Rezonans – otwór może zacząć rezonować dla pewnych długości fali, zwiększając transmisję sygnału.
Częstotliwość odcięcia – czym jest i jak ją liczyć
Pojęcie częstotliwości odcięcia (ang. cutoff frequency) odnosi się do maksymalnej częstotliwości, przy której dany otwór lub szczelina jeszcze skutecznie tłumi fale EM. Powyżej tej częstotliwości ekranowanie staje się nieskuteczne.
Dla prostokątnego otworu w ekranie, przybliżoną częstotliwość odcięcia można oszacować ze wzoru:
f_c ≈ 15 / d
Gdzie:
- f_c – częstotliwość odcięcia w GHz
- d – najdłuższy wymiar otworu w centymetrach
Na przykład: otwór o długości 2 cm przepuszcza fale o częstotliwości powyżej ok. 7,5 GHz.
Dobre praktyki: maksymalne rozmiary otworów vs. długość fali
Aby otwory nie degradowały ekranowania, ich wymiary powinny być znacznie mniejsze niż długość fali, najlepiej mniejsze niż λ/20. Dla częstotliwości 1 GHz (długość fali ok. 30 cm), maksymalna średnica otworu powinna wynosić poniżej 1,5 cm.
Dobre praktyki projektowe obejmują:
- unikanie długich szczelin,
- stosowanie przekładek stykowych i punktów uziemiających (stitching vias),
- ekranowanie szczelin za pomocą materiałów przewodzących (np. uszczelek EMI),
- lokalne uszczelnianie kluczowych punktów wejść/wyjść sygnałowych.
Praktyczne wskazówki projektowe dla PCB
Ekranowanie EMI nie powinno być traktowane jako dodatek na końcowym etapie projektu. Wręcz przeciwnie – najlepsze rezultaty osiąga się wtedy, gdy ochrona przed zakłóceniami elektromagnetycznymi jest integralną częścią procesu projektowania płytki drukowanej już od samego początku.
Dlaczego warto planować ekranowanie już na etapie projektu?
Projektując PCB bez myślenia o EMI, łatwo wpaść w pułapkę „reaktywnego” podejścia – najpierw projektujemy obwód, a dopiero po testach dodajemy ekranowanie tam, gdzie pojawił się problem. Niestety, takie działania są kosztowne, często wymagają przeprojektowania i rzadko zapewniają pełną skuteczność.
Planowanie ekranowania z wyprzedzeniem pozwala:
- zoptymalizować trasowanie sygnałów i rozmieszczenie komponentów,
- dobrać odpowiednią strukturę warstw (np. warstwa masy jako ekran),
- zminimalizować pętle prądowe i sprzężenia między obwodami,
- uwzględnić fizyczne miejsce na metalowe pokrywy lub ekrany folii EMC,
- ograniczyć kosztowne poprawki w późniejszym etapie.
Gotowe rozwiązania od producentów
Na rynku dostępnych jest wiele rozwiązań „z półki”, które ułatwiają wdrażanie ekranowania EMI bez potrzeby samodzielnego projektowania wszystkiego od podstaw. Są to m.in.:
- ekrany lutowane (shield cans) – dostępne w różnych wymiarach, z możliwością stosowania ramek lutowanych SMT,
- uszczelki EMI – przewodzące elementy montowane wzdłuż krawędzi osłon lub obudów, zapewniające kontakt elektryczny,
- folie i taśmy ekranujące – do tymczasowego lub elastycznego ekranowania wybranych obszarów,
- materiały kompozytowe – dla ekranowania obudów z tworzyw sztucznych.
Wybór konkretnego rozwiązania zależy od przestrzeni na PCB, typu zagrożeń EMI, łatwości montażu oraz kosztów produkcji.
Koszty vs. skuteczność – jak zoptymalizować projekt
W projektowaniu ekranowania EMI chodzi o znalezienie balansu między kosztami a efektywnością. Przesadne ekranowanie (np. pełne metalowe klatki dla całej płytki) zwiększa masę, koszty produkcji i trudność montażu – często bez proporcjonalnych korzyści.
Z drugiej strony, zbyt oszczędne podejście (np. poleganie tylko na filtrach lub warstwie masy) może nie wystarczyć w środowiskach o dużym natężeniu zakłóceń.
Optymalizacja obejmuje:
- stosowanie ekranowania tylko tam, gdzie jest to uzasadnione (np. wokół źródeł lub ofiar EMI),
- wykorzystanie istniejących elementów (np. obudowy jako część ekranu),
- wybór efektywnych materiałów (miedź tam, gdzie kluczowe jest odbicie; stal, gdy ważna jest absorpcja),
- użycie tanich, seryjnych komponentów ekranujących od renomowanych dostawców.
Podsumowanie – wnioski dla projektanta elektroniki
Zakłócenia elektromagnetyczne (EMI) stanowią istotne wyzwanie w projektowaniu nowoczesnej elektroniki. Ich obecność może nie tylko pogorszyć działanie urządzeń, ale wręcz uniemożliwić ich prawidłową pracę. Dlatego ekranowanie na poziomie płytki drukowanej jest nie tylko rozsądnym, ale wręcz koniecznym elementem projektowania.
Najważniejsze wnioski i praktyki:
- EMI to problem, z którym trzeba się mierzyć już na etapie projektowania. Nie warto czekać z ekranowaniem do ostatnich testów – planowanie ochrony na poziomie PCB przynosi największe korzyści i minimalizuje koszty.
- Znajomość charakterystyki fal elektromagnetycznych (składniki E i H, impedancja fali) pozwala świadomie dobierać metody i materiały do ekranowania.
- Skuteczność ekranowania zależy od mechanizmu działania: odbicia, absorpcji oraz transmisji fali. Warto rozumieć, kiedy dominuje odbicie (fale elektryczne) i kiedy absorpcja (fale magnetyczne), aby odpowiednio dobierać materiały (np. miedź, stal, mosiądz).
- Projektowanie ekranów EMI wymaga uwzględnienia szczegółów takich jak szczeliny, szwy czy otwory. Ich wielkość i rozkład musi być dopasowany do długości fali, aby nie osłabić skuteczności ekranowania.
- Wybór materiałów i gotowych rozwiązań musi balansować między kosztami a efektywnością. Często nie trzeba pełnych metalowych obudów – wystarczy inteligentne zastosowanie ekranów na poziomie PCB i odpowiednie rozmieszczenie elementów.
- Gotowe komponenty i technologie (np. ekrany lutowane, folie EMC, uszczelki) ułatwiają implementację i przyspieszają proces produkcji.
- Ostatecznie skuteczne ekranowanie na poziomie płytki PCB, często okazuje się bardziej efektywne i ekonomiczne niż próby poprawy EMI dopiero z poziomu obudowy.
Wprowadzenie konsekwentnych, przemyślanych praktyk projektowych w zakresie ochrony EMI pozwala nie tylko spełnić wymogi norm i certyfikatów, ale przede wszystkim zapewnia stabilną, niezawodną pracę urządzeń w trudnych warunkach elektromagnetycznych.
Źródła:
1. Paul, C. R. – Introduction to Electromagnetic Compatibility Kompleksowe wprowadzenie do zagadnień kompatybilności elektromagnetycznej, idealne dla projektantów elektroniki.
2. Ott, H. W. – Electromagnetic Compatibility Engineering Praktyczny przewodnik po metodach projektowania i testowania systemów odpornych na EMI.
3. Pozar, D. M. – Microwave Engineering Książka omawiająca m.in. podstawy propagacji fal elektromagnetycznych i impedancję, bardzo pomocna przy zrozumieniu fizyki EMI.
4. Normy i wytyczne EMC (np. CISPR, EN 55032) Oficjalne dokumenty regulujące wymagania dotyczące emisji i odporności elektromagnetycznej urządzeń.
5. Materiały techniczne producentów materiałów ekranowych (np. 3M, Laird, TC Shielding, TEMAS) Szczegółowe dane dotyczące właściwości różnych materiałów do ekranowania EMI oraz przykłady zastosowań.
Dodaj komentarz