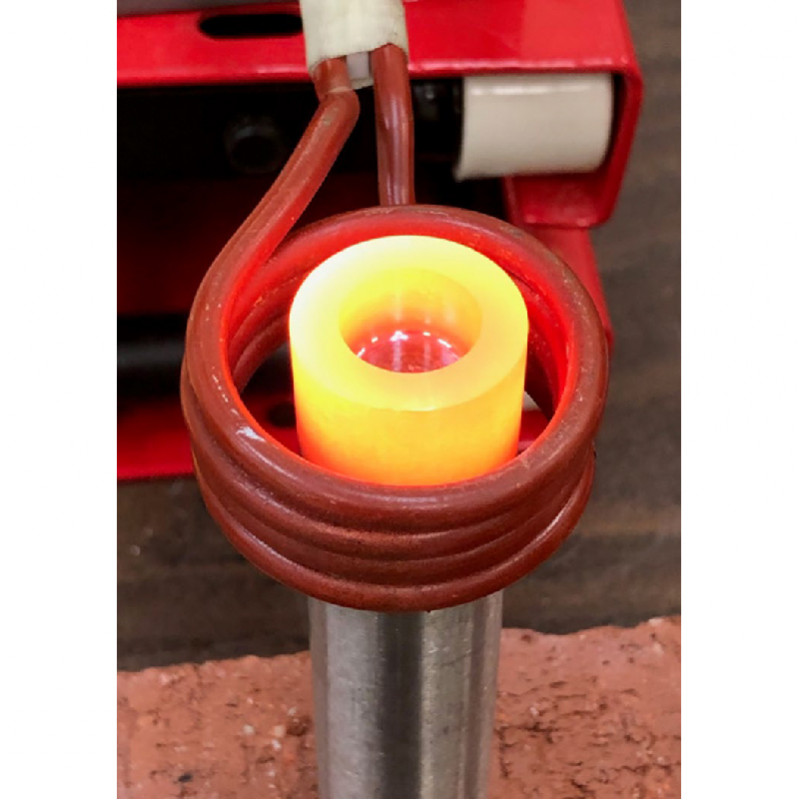
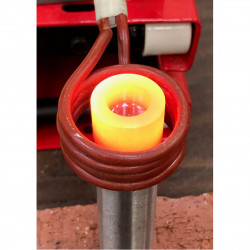
Sie müssen eingeloggt sein
Category
Fotos dienen nur zu Informationszwecken.
please use latin characters
Objective: To heat a steel part for a brazing application; the client is manufacturing steel cable for the aerospace industry.
Frequency: 204 kHz
Material: Steel parts
Temperature: 1400 °F (760 °C)
A custom-designed multiple-turn helical coil was built to generate the required heating for the application. Temperature indicating paint was then applied to the part, which dissolves when the part reaches temperature. It took about 50 seconds to heat the part to temperature. The client was updating their induction system and this meets their time objectives.
Interessieren Sie sich für dieses Produkt? Benötigen Sie zusätzliche Informationen oder individuelle Preise?
Sie müssen eingeloggt sein
Objective: To heat a steel part for a brazing application; the client is manufacturing steel cable for the aerospace industry.
Frequency: 204 kHz
Material: Steel parts
Temperature: 1400 °F (760 °C)
A custom-designed multiple-turn helical coil was built to generate the required heating for the application. Temperature indicating paint was then applied to the part, which dissolves when the part reaches temperature. It took about 50 seconds to heat the part to temperature. The client was updating their induction system and this meets their time objectives.
Your review appreciation cannot be sent
Report comment
Report sent
Your report cannot be sent
Eigenen Kommentar verfassen
Review sent
Your review cannot be sent