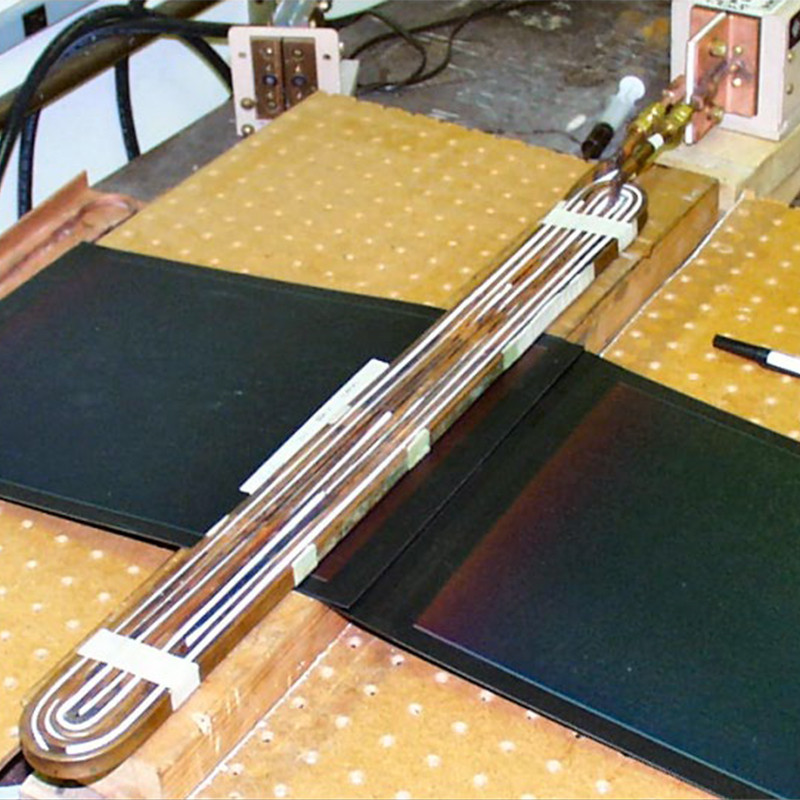
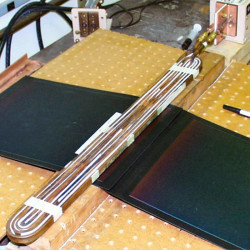
Category
Photos are for informational purposes only. View product specification
please use latin characters
Objective: To heat the stainless-steel substrate of a solar panel shingle in order to melt the polymer encapsulant, allowing two shingles to bond together with a 3-inch (76.2 mm) overlap.
Equipment: Ambrell EASYHEAT 1.2 kW, 150-400 kHz solid state induction power supply with a workhead and coil specifically designed for this application.ania.
Frequency: 166 kHz
Material: 3" (76.2 mm) by 10.25" (260.4 mm) section of a 21" (533.4 mm) solar panel shingle
Temperature: 266 °F (130 °C)
Testing: Stationary heating, with the coil located on the topside of the sample, was utilized to achieve uniform melt and adhesion. The shingles were overlapped according to requirements and placed on wood to simulate the installation on a roofing surface. In addition, pressure was applied by pressing the water-cooled coil against the shingle to facilitate the bonding. Tests were performed at several time-voltage settings. Testing resulted in excellent bond formation with the absence of encapsulant bubbling and only slight surface texture change.
Benefits:
Are you interested in this product? Do you need additional information or individual pricing?
Objective: To heat the stainless-steel substrate of a solar panel shingle in order to melt the polymer encapsulant, allowing two shingles to bond together with a 3-inch (76.2 mm) overlap.
Equipment: Ambrell EASYHEAT 1.2 kW, 150-400 kHz solid state induction power supply with a workhead and coil specifically designed for this application.ania.
Frequency: 166 kHz
Material: 3" (76.2 mm) by 10.25" (260.4 mm) section of a 21" (533.4 mm) solar panel shingle
Temperature: 266 °F (130 °C)
Testing: Stationary heating, with the coil located on the topside of the sample, was utilized to achieve uniform melt and adhesion. The shingles were overlapped according to requirements and placed on wood to simulate the installation on a roofing surface. In addition, pressure was applied by pressing the water-cooled coil against the shingle to facilitate the bonding. Tests were performed at several time-voltage settings. Testing resulted in excellent bond formation with the absence of encapsulant bubbling and only slight surface texture change.
Benefits:
Your review appreciation cannot be sent
Report comment
Report sent
Your report cannot be sent
Write your review
Review sent
Your review cannot be sent