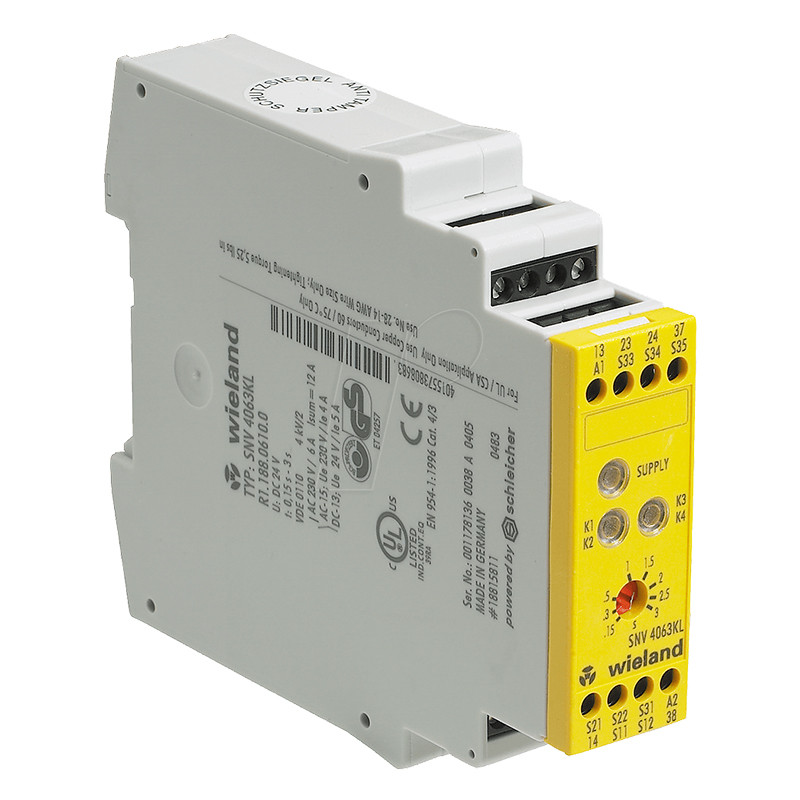
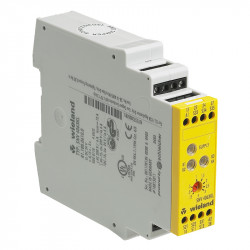
Category
Photos are for informational purposes only. View product specification
please use latin characters
Base device for single-channel or two-channel emergency stop and
safety gate applications
• Stop category 0 / 1 according to EN 60204-1
• Applications up to safety category 4 according to EN 954-1
• Safety category of the device: 4 (undelayed contacts) /
3 (delayed contacts) according to EN 954-1
• OFF-delay time adjustable in the range 0.15 to 3 s or 1.5 to 30 s
• Control through contacts or semiconductors
• Reset button monitoring, cross monitoring, synchrocheck
• 3 enabling current paths (2 undelayed, 1 OFF-delayed
![]() |
A1 / A2, supply voltage, SUPPLY LED S12 emergency stop channel 1 S31 / S22 emergency stop channel 2 S34 reset rising edge 13/14,23/24,LED K1/K2 37/38, LED K3/K4 tM = minimum ON time tA = response time tR1 = release time tR2 = OFF-delay time (selectable) TW = recovery time |
![]() |
A1/A2 supply voltage, SUPPLY LED S12 channel 1 S31/S22 emergency stop channel 2 S34 reset rising edge 13/14,23/24,LED K1/K2 37/38, LED K3/K4 tM = minimum ON time tA = response time tR1 = release time tR2 = OFF-delay time (selectable) TW = recovery time |
Description/number | ||||
---|---|---|---|---|
type | Turn off delay | Nominal voltage | Terminals | number pce/package. |
SNV 4063K | 3 s | DC 24V | screw terminals | R1.188.0610.0 1 |
30 s | DC 24V | screw terminals | R1.188.0630.0 1 | |
SNV 4063KL-A | 3 s | DC 24V | screw plug terminals | R1.188.0620.0 1 |
30 s | DC 24V | screw plug terminals | R1.188.0640.0 1 |
Technical data | SNV 4063KL | |||
---|---|---|---|---|
Function according to EN 60204-1
|
Emergency stop relay for controlled stop
|
|||
Function display
|
3 LEDs green
|
|||
Function diagram
|
FD 221-11-1 W, FD 221-11-2 W
|
|||
Power supply circuit
|
min
|
type
|
max
|
|
Rated voltage Un
|
AC/DC 20,4 V
|
AC/DC 24 V
|
AC/DC 26,4 V
|
|
Rated consumption DC
|
2,6 W
|
|||
Residual ripple Uss
|
2,4 V
|
|||
Control circuit
|
||||
Rated output voltage S11/ S33
for supply of inputs S34, S35, S12, S31, S22
|
DC 22 V
|
|||
Response time / recovery time Fuse (PTC thermistor)
|
2 s/3 s
|
|||
Rated current / peak current S12
|
25 mA/50 mA
|
|||
Rated current / peak current S31, S22
|
25 mA/100 mA
|
|||
Rated current / peak current S34, S35
|
40 mA/50 mA
|
|||
Response time tA1(with reset button monitoring) on S34
|
30 ms
|
|||
Response time tA2(without reset button monitoring) on S35
|
700 ms
|
|||
Release time tR1 K1, K2 with emergency stop
|
25 ms
|
|||
Release time tR2 K3, K4 (2 setting ranges, infinitely adjustable, unbuffered)
|
0,15 s ±16%
1,5 s ±16% |
3 s ±16%
30 s ±16% |
||
Minimum ON time tM S33-S34
|
200 ms
|
3 s
|
||
ON time tM S33-S35
|
200 ms
|
°°
|
||
Recovery time tW (Start)
|
500 ms
|
|||
Synchronous time tS
|
100 ms
|
500 ms
|
||
Output circuit
|
||||
Contact assignment
|
2 enabling current paths, undelayed, NO contact, positively driven
1 enabling current path, OFF-delayed, NO contact, positively driven
|
|||
Rated operating voltage Un
|
AC/DC 230 V
|
|||
Max. continuous current In per contact
|
6 A
|
|||
Max. total current of all current paths
|
12 A
|
|||
Application category according to EN 60947-5-1
|
AC-15: Ue 230 V AC, Ie 4 A (3600 switching cycles/h)
DC-13: Ue 24 V DC, Ie 5 A (360 switching cycles/h) |
|||
Short-circuit protection, max. fuse insert
|
6 A class gG or circuit breaker with trigger characteristic B or C
|
|||
General data
|
||||
Creepage distances and clearances between the circuits |
according EN 60664-1
|
|||
Rated impulse voltage
|
4 kV
|
|||
Overvoltage category
|
III
|
|||
Degree of pollution of the device: inside / outside
|
2/3
|
|||
Rated voltage
|
AC 300V
|
|||
Protection degree according to DIN EN 60529 (housing / terminals)
|
IP 40/IP 20
|
|||
Ambient temperature / storage temperature
|
-25 - +55 °C/-25 - +75 °C
|
|||
Dimension diagram
|
K 4-1 (screw terminals / K 4-2 (pluggable terminals)
|
|||
Rated cross sections fine-stranded/solid
|
2x0,14 - 0,75 mm2/1x0,14 - 2,5 mm2
|
|||
or fine-stranded with ferrules
|
1x0,25 - 2,5 mm2/2x0,25 - 0,5 mm2
|
|||
Permissible tightening torque
|
0,5 - 0,6 Nm
|
|||
for UL and CSA applications
|
Wire ranges
|
AWG 18-16 only use Cu wires
0.79 in-lbs |
||
Max. tightening torques
|
||||
Weight
|
0,2 kg
|
|||
Accessories
|
-
|
Are you interested in this product? Do you need additional information or individual pricing?
Base device for single-channel or two-channel emergency stop and
safety gate applications
• Stop category 0 / 1 according to EN 60204-1
• Applications up to safety category 4 according to EN 954-1
• Safety category of the device: 4 (undelayed contacts) /
3 (delayed contacts) according to EN 954-1
• OFF-delay time adjustable in the range 0.15 to 3 s or 1.5 to 30 s
• Control through contacts or semiconductors
• Reset button monitoring, cross monitoring, synchrocheck
• 3 enabling current paths (2 undelayed, 1 OFF-delayed
![]() |
A1 / A2, supply voltage, SUPPLY LED S12 emergency stop channel 1 S31 / S22 emergency stop channel 2 S34 reset rising edge 13/14,23/24,LED K1/K2 37/38, LED K3/K4 tM = minimum ON time tA = response time tR1 = release time tR2 = OFF-delay time (selectable) TW = recovery time |
![]() |
A1/A2 supply voltage, SUPPLY LED S12 channel 1 S31/S22 emergency stop channel 2 S34 reset rising edge 13/14,23/24,LED K1/K2 37/38, LED K3/K4 tM = minimum ON time tA = response time tR1 = release time tR2 = OFF-delay time (selectable) TW = recovery time |
Description/number | ||||
---|---|---|---|---|
type | Turn off delay | Nominal voltage | Terminals | number pce/package. |
SNV 4063K | 3 s | DC 24V | screw terminals | R1.188.0610.0 1 |
30 s | DC 24V | screw terminals | R1.188.0630.0 1 | |
SNV 4063KL-A | 3 s | DC 24V | screw plug terminals | R1.188.0620.0 1 |
30 s | DC 24V | screw plug terminals | R1.188.0640.0 1 |
Technical data | SNV 4063KL | |||
---|---|---|---|---|
Function according to EN 60204-1
|
Emergency stop relay for controlled stop
|
|||
Function display
|
3 LEDs green
|
|||
Function diagram
|
FD 221-11-1 W, FD 221-11-2 W
|
|||
Power supply circuit
|
min
|
type
|
max
|
|
Rated voltage Un
|
AC/DC 20,4 V
|
AC/DC 24 V
|
AC/DC 26,4 V
|
|
Rated consumption DC
|
2,6 W
|
|||
Residual ripple Uss
|
2,4 V
|
|||
Control circuit
|
||||
Rated output voltage S11/ S33
for supply of inputs S34, S35, S12, S31, S22
|
DC 22 V
|
|||
Response time / recovery time Fuse (PTC thermistor)
|
2 s/3 s
|
|||
Rated current / peak current S12
|
25 mA/50 mA
|
|||
Rated current / peak current S31, S22
|
25 mA/100 mA
|
|||
Rated current / peak current S34, S35
|
40 mA/50 mA
|
|||
Response time tA1(with reset button monitoring) on S34
|
30 ms
|
|||
Response time tA2(without reset button monitoring) on S35
|
700 ms
|
|||
Release time tR1 K1, K2 with emergency stop
|
25 ms
|
|||
Release time tR2 K3, K4 (2 setting ranges, infinitely adjustable, unbuffered)
|
0,15 s ±16%
1,5 s ±16% |
3 s ±16%
30 s ±16% |
||
Minimum ON time tM S33-S34
|
200 ms
|
3 s
|
||
ON time tM S33-S35
|
200 ms
|
°°
|
||
Recovery time tW (Start)
|
500 ms
|
|||
Synchronous time tS
|
100 ms
|
500 ms
|
||
Output circuit
|
||||
Contact assignment
|
2 enabling current paths, undelayed, NO contact, positively driven
1 enabling current path, OFF-delayed, NO contact, positively driven
|
|||
Rated operating voltage Un
|
AC/DC 230 V
|
|||
Max. continuous current In per contact
|
6 A
|
|||
Max. total current of all current paths
|
12 A
|
|||
Application category according to EN 60947-5-1
|
AC-15: Ue 230 V AC, Ie 4 A (3600 switching cycles/h)
DC-13: Ue 24 V DC, Ie 5 A (360 switching cycles/h) |
|||
Short-circuit protection, max. fuse insert
|
6 A class gG or circuit breaker with trigger characteristic B or C
|
|||
General data
|
||||
Creepage distances and clearances between the circuits |
according EN 60664-1
|
|||
Rated impulse voltage
|
4 kV
|
|||
Overvoltage category
|
III
|
|||
Degree of pollution of the device: inside / outside
|
2/3
|
|||
Rated voltage
|
AC 300V
|
|||
Protection degree according to DIN EN 60529 (housing / terminals)
|
IP 40/IP 20
|
|||
Ambient temperature / storage temperature
|
-25 - +55 °C/-25 - +75 °C
|
|||
Dimension diagram
|
K 4-1 (screw terminals / K 4-2 (pluggable terminals)
|
|||
Rated cross sections fine-stranded/solid
|
2x0,14 - 0,75 mm2/1x0,14 - 2,5 mm2
|
|||
or fine-stranded with ferrules
|
1x0,25 - 2,5 mm2/2x0,25 - 0,5 mm2
|
|||
Permissible tightening torque
|
0,5 - 0,6 Nm
|
|||
for UL and CSA applications
|
Wire ranges
|
AWG 18-16 only use Cu wires
0.79 in-lbs |
||
Max. tightening torques
|
||||
Weight
|
0,2 kg
|
|||
Accessories
|
-
|
Your review appreciation cannot be sent
Report comment
Report sent
Your report cannot be sent
Write your review
Review sent
Your review cannot be sent