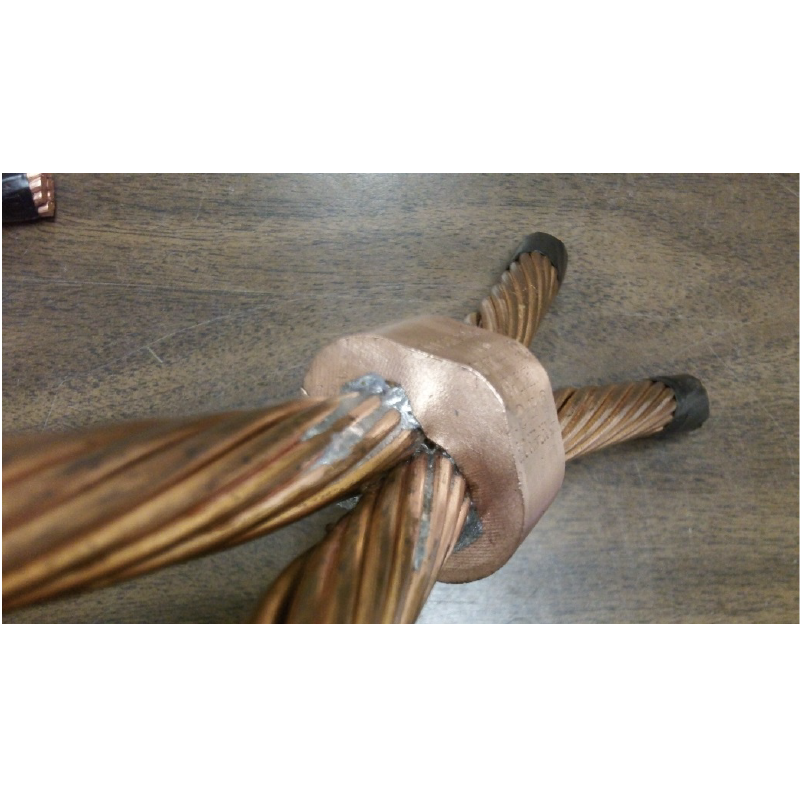
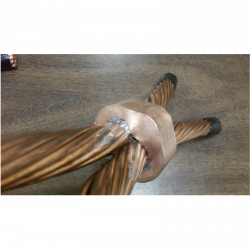
Category
Photos are for informational purposes only. View product specification
please use latin characters
Objective: To heat a copper lug and a wire to temperature for a soldering application to create grounding connections.
Frequency: 109 kHz
Material: Wire and lug
Temperature: 370 °F (188 °C)
The parts were fluxed and the solder wire was folded two times and twisted to enable a greater feed rate. The assembly was then placed in the coil and the power was turned on. The coil was designed to focus heat on the large lug and to keep solder from running over the wires. After 40 seconds, the assembly reached soldering temperature.
It was observed that the lug could easily be filled with solder when it’s placed in a vertical direction and the solder will run out of the bottom when full. If the lug was oriented in a horizontal position the solder could be more readily kept in and around the lug.
Are you interested in this product? Do you need additional information or individual pricing?
Objective: To heat a copper lug and a wire to temperature for a soldering application to create grounding connections.
Frequency: 109 kHz
Material: Wire and lug
Temperature: 370 °F (188 °C)
The parts were fluxed and the solder wire was folded two times and twisted to enable a greater feed rate. The assembly was then placed in the coil and the power was turned on. The coil was designed to focus heat on the large lug and to keep solder from running over the wires. After 40 seconds, the assembly reached soldering temperature.
It was observed that the lug could easily be filled with solder when it’s placed in a vertical direction and the solder will run out of the bottom when full. If the lug was oriented in a horizontal position the solder could be more readily kept in and around the lug.
Your review appreciation cannot be sent
Report comment
Report sent
Your report cannot be sent
Write your review
Review sent
Your review cannot be sent