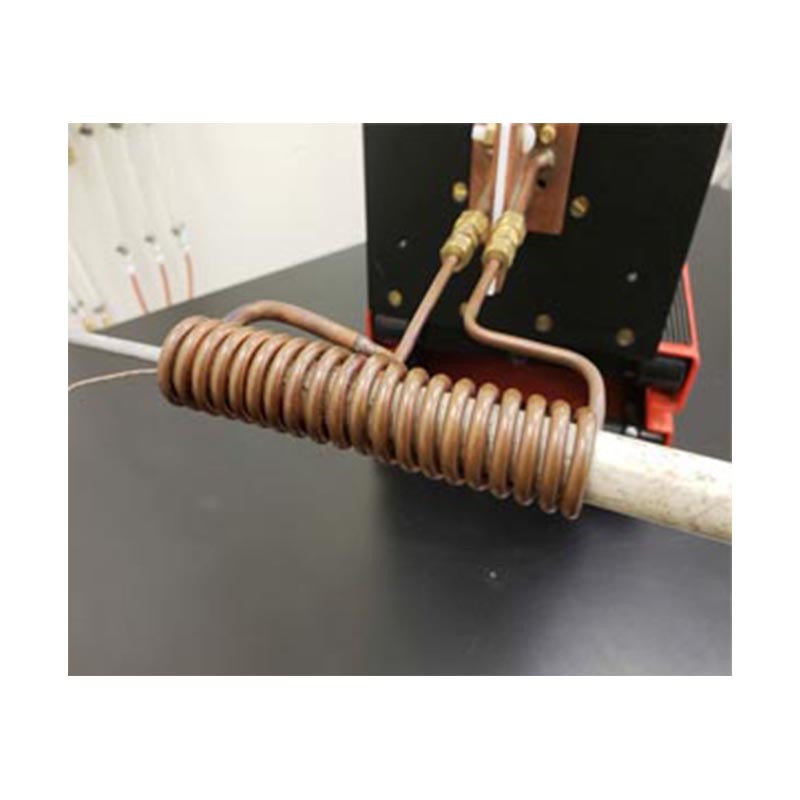
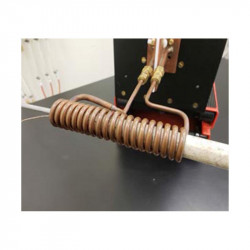
Category
Photos are for informational purposes only. View product specification
please use latin characters
Objective: Preheating steel wire before hot heading to create a screw; they wanted to switch from cold heading to extend tool life.
Equipment: Ambrell EKOHEATⓇ 30 kW, 50-150 kHz solid state induction power supply with a workhead and coil specifically designed for this application.
Frequency: 94 kHz
Material: Steel wire (0.214” / 5.4 mm diameter)
Temperature: 350 °F (177 °C)
Testing:
Benefits:
Are you interested in this product? Do you need additional information or individual pricing?
Objective: Preheating steel wire before hot heading to create a screw; they wanted to switch from cold heading to extend tool life.
Equipment: Ambrell EKOHEATⓇ 30 kW, 50-150 kHz solid state induction power supply with a workhead and coil specifically designed for this application.
Frequency: 94 kHz
Material: Steel wire (0.214” / 5.4 mm diameter)
Temperature: 350 °F (177 °C)
Testing:
Benefits:
Your review appreciation cannot be sent
Report comment
Report sent
Your report cannot be sent
Write your review
Review sent
Your review cannot be sent