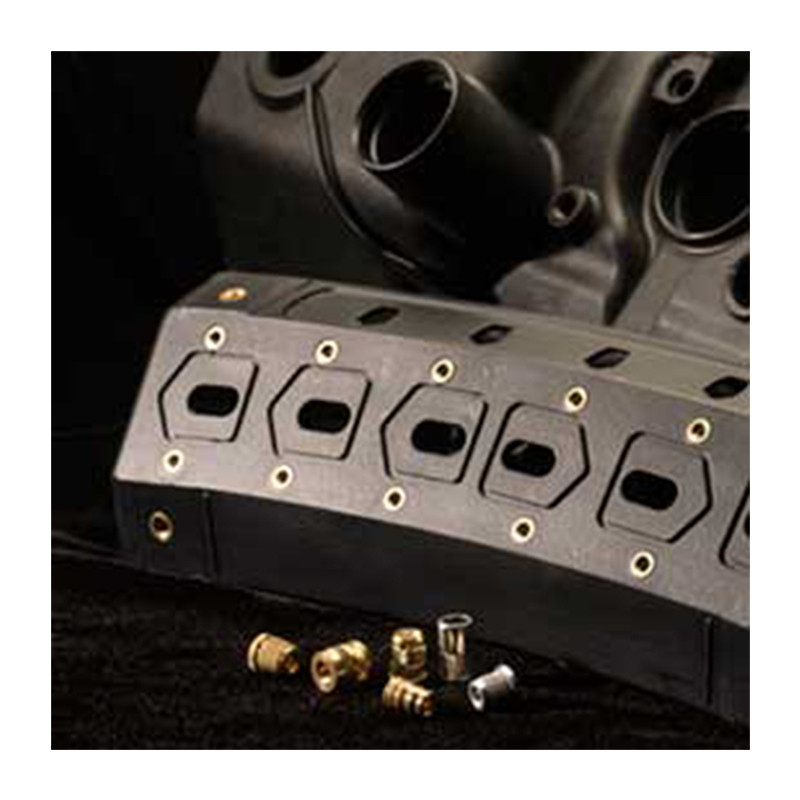
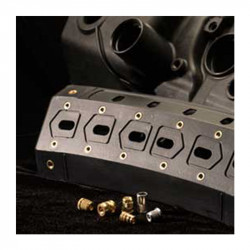
Category
Photos are for informational purposes only. View product specification
please use latin characters
A large number of polymeric materials come under the plastic classification. Polyethylene, polypropylene, polyvinyl chloride, polystyrene, and the fluorocarbons, epoxies, phenolics, and polyester may all be classified as plastics. When viewed as a whole, plastics have a wide variety of combinations of properties. Some are very rigid and brittle; others are flexible, exhibiting both elastic and plastic deformations when stressed, and sometimes experiencing considerable deformation before fracture. Plastic components may also contain glass particles, various fibers, or other polymers.
Plastic reflow involves any process where the plastic becomes liquid, which including a wide range of applications from metal reclaiming to thermoplastic composites manufacture.
Modern induction heatingprovides reliable, repeatable, non-contact and energy-efficient heat in a minimal amount of time. Solid state systems are capable of heating very small areas within precise production tolerances, without disturbing individual metallurgical characteristics.
Induction heating has great potential in the area of plastic reflow because of the controlled rapid application of heat. However, one hurdle must be cleared in order for induction to work; plastics do not conduct current.
Non-conductive materials can often be heated very effectively by using a conductive metal susceptor to transfer the heat, or by placing conductive fibers or powder within the plastic itself. Heating potential in all of the above scenarios is solely based on the concentration and type of conductive material. If a powder is too fine or at too small of a concentration, then the particles will not be affected by the field and eddy currents will not form.
Induction systems typically used for plastic reflow range from 1 to 10kW, depending on the parts and application requirements.
Are you interested in this product? Do you need additional information or individual pricing?
A large number of polymeric materials come under the plastic classification. Polyethylene, polypropylene, polyvinyl chloride, polystyrene, and the fluorocarbons, epoxies, phenolics, and polyester may all be classified as plastics. When viewed as a whole, plastics have a wide variety of combinations of properties. Some are very rigid and brittle; others are flexible, exhibiting both elastic and plastic deformations when stressed, and sometimes experiencing considerable deformation before fracture. Plastic components may also contain glass particles, various fibers, or other polymers.
Plastic reflow involves any process where the plastic becomes liquid, which including a wide range of applications from metal reclaiming to thermoplastic composites manufacture.
Modern induction heatingprovides reliable, repeatable, non-contact and energy-efficient heat in a minimal amount of time. Solid state systems are capable of heating very small areas within precise production tolerances, without disturbing individual metallurgical characteristics.
Induction heating has great potential in the area of plastic reflow because of the controlled rapid application of heat. However, one hurdle must be cleared in order for induction to work; plastics do not conduct current.
Non-conductive materials can often be heated very effectively by using a conductive metal susceptor to transfer the heat, or by placing conductive fibers or powder within the plastic itself. Heating potential in all of the above scenarios is solely based on the concentration and type of conductive material. If a powder is too fine or at too small of a concentration, then the particles will not be affected by the field and eddy currents will not form.
Induction systems typically used for plastic reflow range from 1 to 10kW, depending on the parts and application requirements.
Your review appreciation cannot be sent
Report comment
Report sent
Your report cannot be sent
Write your review
Review sent
Your review cannot be sent