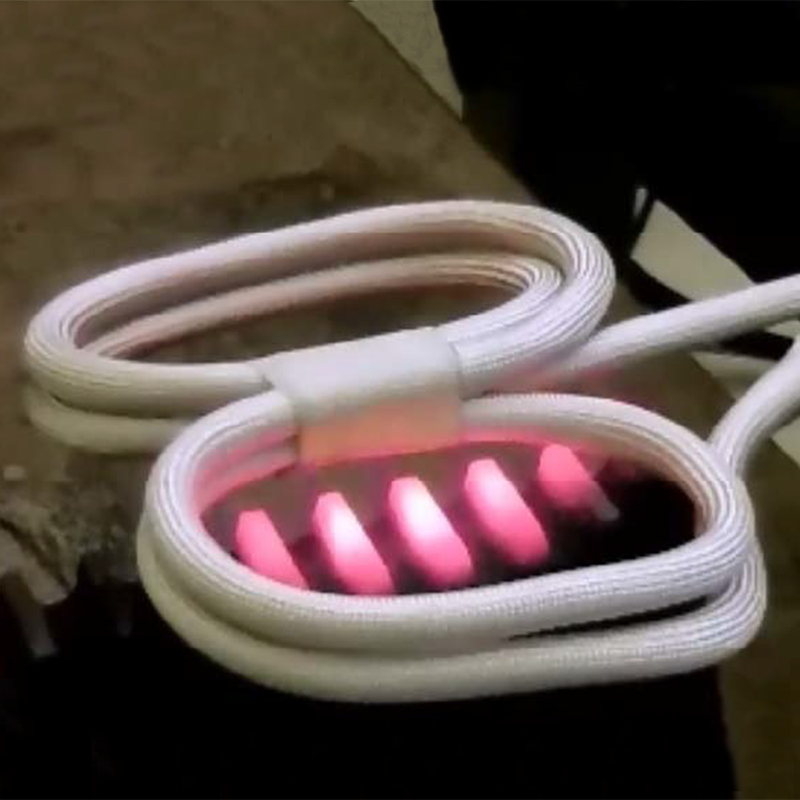
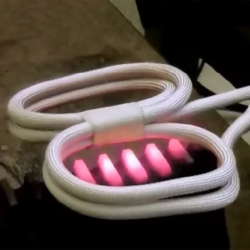
Category
Photos are for informational purposes only. View product specification
please use latin characters
Objective: Heating the teeth of a large saw blade for a hardening application; the objective is to reduce the heating time.
Equipment:
Frequency: 134 kHz
Material:
Temperature: 1650 ºF (899 ºC)
Testing:
Benefits:
Are you interested in this product? Do you need additional information or individual pricing?
Objective: Heating the teeth of a large saw blade for a hardening application; the objective is to reduce the heating time.
Equipment:
Frequency: 134 kHz
Material:
Temperature: 1650 ºF (899 ºC)
Testing:
Benefits:
Your review appreciation cannot be sent
Report comment
Report sent
Your report cannot be sent
Write your review
Review sent
Your review cannot be sent