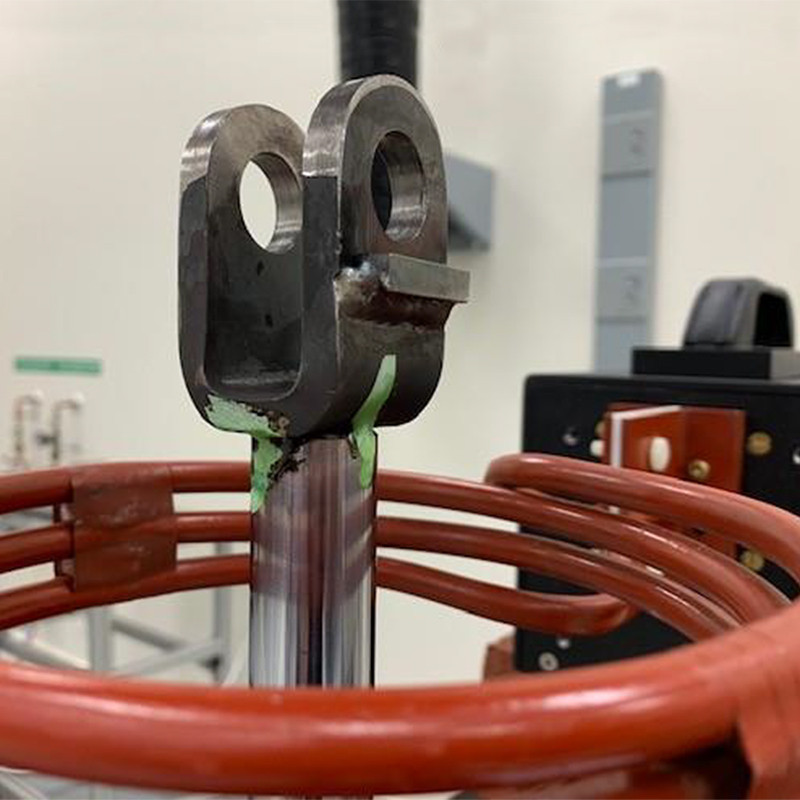
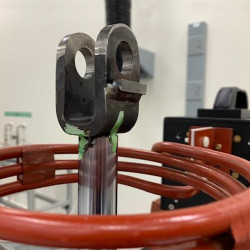
Category
Photos are for informational purposes only. View product specification
please use latin characters
Objective: To preheat steel rod assemblies for welding.
Background: This is an automotive industry application. The client had been using torches for preheating. However, due to process improvements thanks to new automation in their facility, torch heating became too slow. This resulted in a backlog that kept them from maximizing their throughput.
Frequency: 109 kHz
Equipment:
Material: Multiple magnetic steel assemblies
Temperature: 400 ºF (204 ºC)
Process:
Temperature indicating paint was applied to the part, which dissolves when the part reaches the target temperature. It took 45 to 75 seconds to heat each part to temperature, depending on part size. The height of the coil relative to the joint area is a critical consideration for this application. The distance impacts how uniformly both sides of the joint heat.
Benefits:
Are you interested in this product? Do you need additional information or individual pricing?
Objective: To preheat steel rod assemblies for welding.
Background: This is an automotive industry application. The client had been using torches for preheating. However, due to process improvements thanks to new automation in their facility, torch heating became too slow. This resulted in a backlog that kept them from maximizing their throughput.
Frequency: 109 kHz
Equipment:
Material: Multiple magnetic steel assemblies
Temperature: 400 ºF (204 ºC)
Process:
Temperature indicating paint was applied to the part, which dissolves when the part reaches the target temperature. It took 45 to 75 seconds to heat each part to temperature, depending on part size. The height of the coil relative to the joint area is a critical consideration for this application. The distance impacts how uniformly both sides of the joint heat.
Benefits:
Your review appreciation cannot be sent
Report comment
Report sent
Your report cannot be sent
Write your review
Review sent
Your review cannot be sent