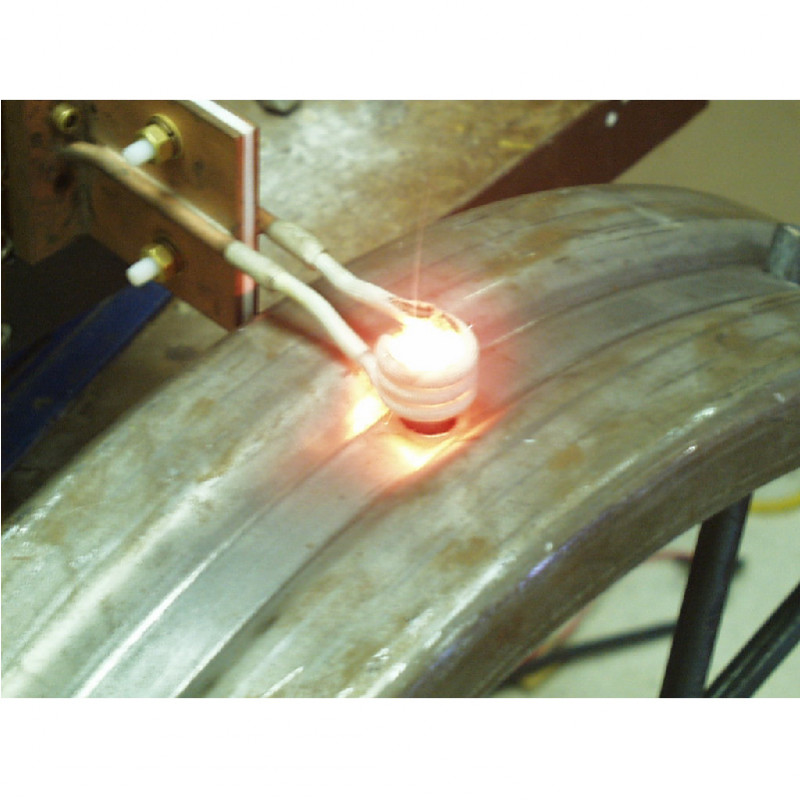
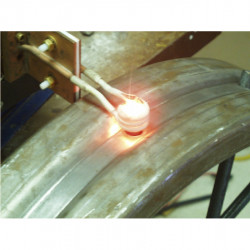
Category
Photos are for informational purposes only. View product specification
please use latin characters
Objective: To heat magnetic steel pins (spokes) for forging on a rim without heat treating and weakening the rim. Previously, a torch was utilized and the heating time was 20 seconds.
Frequency: 294 kHz
Material: 9/16” (14 mm) steel pins.
Temperature: 2000 °F (1093 °C)
A single position three-turn helical coil was used, and the part was placed under the coil. The part was heated to the desired temperature within just seven seconds.
Are you interested in this product? Do you need additional information or individual pricing?
Objective: To heat magnetic steel pins (spokes) for forging on a rim without heat treating and weakening the rim. Previously, a torch was utilized and the heating time was 20 seconds.
Frequency: 294 kHz
Material: 9/16” (14 mm) steel pins.
Temperature: 2000 °F (1093 °C)
A single position three-turn helical coil was used, and the part was placed under the coil. The part was heated to the desired temperature within just seven seconds.
Your review appreciation cannot be sent
Report comment
Report sent
Your report cannot be sent
Write your review
Review sent
Your review cannot be sent