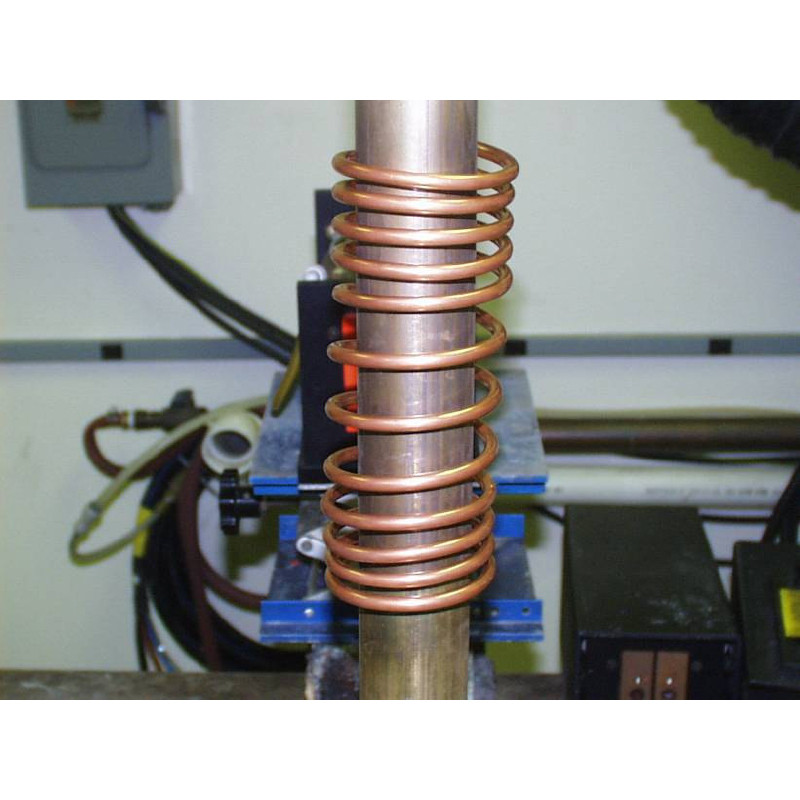
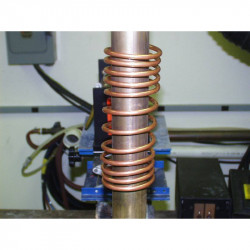
Category
Photos are for informational purposes only. View product specification
please use latin characters
Objective: Annealing brass and bronze tubing for bending in a mandrel bender to form handrails.
Frequency: 228 kHz
Temperature: 1000 °F (538 °C)
A twelve turn helical coil is used to heat an 8” (20.3cm) area 3” (7.6cm) above the end of the tube. Each of the four tubes require a different heat cycle and time to reach the required temperature. Please see the chart below for each tube.
1.5" | 1.5" | 2" | 2" | |
Brass | Bronze | Brass | Bronze | |
Heat Cycle Time [s] | 80 | 100 | 100 | 120 |
Power [kW] | 4 | 4.15 | 3.1 | 3.4 |
Current [A] | 248 | 255 | 200 | 212 |
Frequency [kHz] | 197 | 197 | 228 | 228 |
Are you interested in this product? Do you need additional information or individual pricing?
Objective: Annealing brass and bronze tubing for bending in a mandrel bender to form handrails.
Frequency: 228 kHz
Temperature: 1000 °F (538 °C)
A twelve turn helical coil is used to heat an 8” (20.3cm) area 3” (7.6cm) above the end of the tube. Each of the four tubes require a different heat cycle and time to reach the required temperature. Please see the chart below for each tube.
1.5" | 1.5" | 2" | 2" | |
Brass | Bronze | Brass | Bronze | |
Heat Cycle Time [s] | 80 | 100 | 100 | 120 |
Power [kW] | 4 | 4.15 | 3.1 | 3.4 |
Current [A] | 248 | 255 | 200 | 212 |
Frequency [kHz] | 197 | 197 | 228 | 228 |
Your review appreciation cannot be sent
Report comment
Report sent
Your report cannot be sent
Write your review
Review sent
Your review cannot be sent