-
BackX
-
Components
-
-
Category
-
Semiconductors
- Diodes
- Thyristors
-
Electro-insulated Modules
- Electro-insulated Modules | VISHAY (IR)
- Electro-insulated Modules | INFINEON (EUPEC)
- Electro-insulated Modules | Semikron
- Electro-insulated Modules | POWEREX
- Electro-insulated Modules | IXYS
- Electro-insulated Modules | POSEICO
- Electro-insulated Modules | ABB
- Electro-insulated Modules | TECHSEM
- Go to the subcategory
- Bridge Rectifiers
-
Transistors
- Transistors | GeneSiC
- SiC MOSFET Modules | Mitsubishi
- SiC MOSFET Modules | STARPOWER
- Module SiC MOSFET ABB’s
- IGBT Modules | MITSUBISHI
- Transistor Modules | MITSUBISHI
- MOSFET Modules | MITSUBISHI
- Transistor Modules | ABB
- IGBT Modules | POWEREX
- IGBT Modules | INFINEON (EUPEC)
- Silicon Carbide (SiC) semiconductor elements
- Go to the subcategory
- Gate Drivers
- Power Blocks
- Go to the subcategory
- Electrical Transducers
-
Passive components (capacitors, resistors, fuses, filters)
- Resistors
-
Fuses
- Miniature Fuses for electronic circuits - ABC & AGC Series
- Tubular Fast-acting Fuses
- Time-delay Fuse Links with GL/GG & AM characteristics
- Ultrafast Fuse Links
- Fast-acting Fuses (British & American standard)
- Fast-acting Fuses (European standard)
- Traction Fuses
- High-voltage Fuse Links
- Go to the subcategory
- Capacitors
- EMI Filters
- Supercapacitors
- Power surge protection
- TEMPEST emission revealing filters
- Go to the subcategory
-
Relays and Contactors
- Relays and Contactors - Theory
- 3-Phase AC Semiconductor Relays
- DC Semiconductor Relays
- Controllers, Control Systems and Accessories
- Soft Starters and Reversible Relays
- Electromechanical Relays
- Contactors
- Rotary Switches
-
Single-Phase AC Semiconductor Relays
- AC ONE PHASE RELAYS 1 series| D2425 | D2450
- One phase semiconductor AC relays CWA and CWD series
- One phase semiconductor AC relays CMRA and CMRD series
- One phase semiconductor AC relays - PS series
- Double and quadruple semiconductor AC relays - D24 D, TD24 Q, H12D48 D series
- One phase semiconductor relays - gn series
- Ckr series single phase solid state relays
- One phase AC semiconductor relays for DIN bus - ERDA I ERAA series
- 150A AC single phase relays
- Rail Mountable Solid State Relays With Integrated Heat Sink - ENDA, ERDA1 / ERAA1 series
- Go to the subcategory
- Single-Phase AC Semiconductor Relays for PCBs
- Interface Relays
- Go to the subcategory
- Cores and Other Inductive Components
- Heatsinks, Varistors, Thermal Protection
- Fans
- Air Conditioning, Accessories for Electrical Cabinets, Coolers
-
Batteries, Chargers, Buffer Power Supplies and Inverters
- Batteries, Chargers - Theoretical Description
- Modular Li-ion Battery Building Blocks, Custom Batteries, BMS
- Batteries
- Battery Chargers and Accessories
- Uninterruptible Power Supply and Buffer Power Supplies
- Inverters and Photovoltaic Equipments
- Energy storage
- Fuel cells
- Lithium-ion batteries
- Go to the subcategory
-
Automatics
- Futaba Drone Parts
- Limit Switches, Microswitches
- Sensors, Transducers
-
Infrared Thermometers (Pyrometers)
- IR-TE Series - Water-proof Palm-sized Radiation Thermometer
- IR-TA Series - Handheld Type Radiation Thermometer
- IR-H Series - Handheld Type Radiation Thermometer
- IR-BA Series - High-speed Compact Radiation Thermometer
- IR-FA Series - Fiber Optic Radiation Thermometer
- IR-BZ Series - Compact Infrared Thermometers
- Go to the subcategory
- Counters, Time Relays, Panel Meters
- Industrial Protection Devices
- Light and Sound Signalling
- Thermographic Camera
- LED Displays
- Control Equipments
- Go to the subcategory
-
Cables, Litz wires, Conduits, Flexible connections
- Wires
- Cable feedthroughs and couplers
- Litz wires
- Cables for extreme applications
- Sleevings
-
Braids
- Flat Braids
- Round Braids
- Very Flexible Flat Braids
- Very Flexible Round Braids
- Cylindrical Cooper Braids
- Cylindrical Cooper Braids and Sleevings
- Flexible Earthing Connections
- Galvanized and Stainless Steel Cylindrical Braids
- PCV Insulated Copper Braids (temp. up to 85C)
- Flat Aluminium Braids
- Junction Set - Braids and Tubes
- Go to the subcategory
- Traction Equipment
- Cable Terminals
- Flexible Insulated Busbars
- Flexible Multilayer Busbars
- Cable Duct Systems
- Go to the subcategory
- View all categories
-
Semiconductors
-
-
- Suppliers
-
Applications
- CNC Machine Tools
- DC and AC Drives (Inverters)
- Energetics
- Energy bank
- Equipment and Components for Hazardous Areas [Ex]
- Equipment for Distribution, Control and Telecommunications Cabinets
- HVAC Automation
- Induction Heating
- Industrial Automation
- Industrial Protective Devices
- Machines for Drying and Wood Processing
- Machines for Thermoforming Plastics
- Mining, Metallurgy and Foundry
- Motors and Transformers
- Power Supplies (UPS) and Rectifier Systems
- Printing
- Temperature Measurement and Regulation
- Test and Laboratory Measurements
- Tram and Railway Traction
- Welding Machines
-
Assembly
-
-
Inductors
-
-
Induction devices
-
-
Service
-
- Contact
- Zobacz wszystkie kategorie
Kompleksowe usługi w zakresie ochrony elektroniki
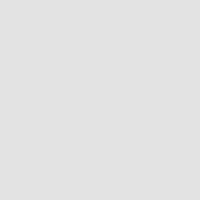
Prowadzenie projektu od wstępnych założeń po finalny produkt jest obecnie tym, czego potrzebuje rynek w zakresie elektroniki przemysłowej.
DACPOL doradza klientom już na poziomie pomysłu i prowadzi ich krok po kroku. Począwszy od doboru ochrony mechanicznej czyli obudowy przez doradztwo w zakresie potencjalnego uszczelnienia urządzenia pod katem zakłóceń RFI, ochrony środowiskowej, rozwiązań interfejsowych i pomoc pod kątem problemu odprowadzenia ciepła aż po wykonanie montażu wstępnego.
ETAP I – ochrona mechaniczna
Rodzinę obudów przemysłowych stanowi obecnie bardzo wiele różnorodnych serii, począwszy od wyrobów z tworzywa sztucznego (ABS, poliwęglan (PC), polistyren, poliester etc.) przez typowe wersję aluminiowe i szafy ze stali nierdzewnej, aż po wykonanie kwasoodporne i przeciwwybuchowe. Podział ze względu na materiał wykonania jest jednym z najczęściej stosowanych, lecz równie ważne jest zastosowanie. Z tego punktu widzenia, technologia 19” stanowi część szeroko pojętych obudów aluminiowych przeznaczonych do zabudowy systemów elektroniki.
Sama nazwa „technologia 19 cali” odnosi się do szerokości panelu przedniego obudowy (19 x 25,4 mm = 482,6 mm), jednak oprócz tego podawana jest również szerokość użytkowa obudowy, która jest oznaczana w sposób zależny od producenta: 84H lub 84E. Obudowy systemu 19 cali mają określoną maksymalną szerokość zewnętrzną wynoszącą 450 mm, która jest uwarunkowana wewnętrzną szerokością szafy rack. Liczby 84 oznaczają ilość jednostek szerokości H lub E. Jednostka szerokości H lub E wynosi dokładnie 5,08 mm i oznacza rozstaw oraz ilość otworów montażowych do zamocowania szyn do płytek PCB lub frontów paneli. Podsumowując, szerokość użytkowa obudowy 19 cali (84H) wynosi 84*5,08 mm = 426,72 mm.
Mając określony jeden z parametrów jako standardowy, często można już na tym etapie przystąpić do projektowania fragmentu instalacji wykorzystującej mechanikę 19”. Głównymi użytkownikami tego rodzaju rozwiązań jest przemysł maszynowy, branża pomiarowa, produkcja elektroniki i płytek PCB, przemysł lotniczy, kolejnictwo oraz przemysł obronny. Niektóre z zastosowań wymagają skonstruowania nietypowych rozwiązań, ale w porozumieniu z dostawcami modułów elektronicznych lub innych podzespołów, które mają być zabudowane wewnątrz szaf rackowych, istnieje możliwość sprostania najbardziej wymagającym warunkom przyszłej pracy. Istotną cechą jest tu atest związany z badaniami na wytrzymałość na wibracje i wstrząsy zgodny z IEC 61 587-1 na podstawie norm IEC 600-68-2-6 oraz normy IEC 600-68-2-27.
Kolejnym oznaczeniem w systemie 19 cali jest wysokość zewnętrzna obudowy U. Literę tę można uznać jako jednostkę wysokości, tzn. 1U = 44,45mm. Podając w oznaczeniu wysokość 1U, 2U, 3U, 4U, 5U, 6U podawana jest wielokrotność tej jednostki, czyli obudowa 6U ma wysokość 6*44,45 = 266,7 mm. Głębokość obudów nie jest ściśle określona przez normy, ale najczęściej stosowane głębokości wynoszą 200, 250 bądź 300 mm.
Typowa budowa systemu 19"
Typowa budowa systemu zabudowy elektroniki wygląda następująco: rama nośna kart, blachy pokrywy, szyny łączące oraz inne pojedyncze części montażowe. Wykonanie poszczególnych powierzchni:
- ściany boczne – wykonane z gładkiego aluminium o grubości 2 mm,
- szyny łączące – profil wytłaczany z aluminium odpornego na korozję,
- płyty kołnierzowe – anodyzowane.
Ze względu na typowo mechaniczną problematykę, która pojawia się przy okazji systemów 19-calowych, niewielu producentów oferuje pełen zakres usług. Bardzo często firmy ograniczają się do dostawy komponentów bazując na podanych wcześniej numerach produktowych – i nic ponadto. Pod tym względem DACPOL jest partnerem, która wychodzi przed szereg, ponieważ oferuje kompletne rozwiązania dla instytucji i firm zajmujących się projektowaniem płytek PCB. Dotyczy to zarówno pojedynczych prototypów, jak i produkcji seryjnej. Podstawowa płytka PCB, z jaką zwraca się do nas klient może być rozbudowana o wiele elementów aż do etapu całego, nowego urządzenia.
- Połączenie płytki PCB z panelem i uchwytem tworzy moduł,
- Moduł umieszczany jest w subracku,
- Subrack, po dobraniu pokryw i paneli, może przechowywać moduły i staje się rackiem,
- Obudowę rackową można rozbudować o uchwyty, elementy montażowe lub dokonać obróbki poszczególnych części na życzenie użytkownika.
ETAP II – ochrona EMC i/lub środowiskowa
Ochrona EMC wiąże się z doborem odpowiednich uszczelek ograniczających wpływ składowej elektrycznej i magnetycznej prądu elektrycznego na funkcjonowanie układu. Uszczelki różnią się między sobą materiałami, wykonaniem, kształtem, tłumieniem oraz innymi parametrami. Decyzja odnośnie wyboru polega na uwzględnieniu nie tylko wymagań elektrycznych, ale także środowiskowych i mechanicznych np. ograniczonej przestrzeni wewnątrz obudowy z urządzeniem.
Jako DACPOL oferujemy szeroki wachlarz uszczelek dzięki czemu jesteśmy w stanie sprostać nawet najwyższym wymaganiom użytkowników. Przykładem są badania typu Tempest zajmujące się falami elektromagnetycznymi emitowanymi przez urządzenia zarówno w formie promieniowania, jak i przewodzenia. Innym aspektem tego rodzaju ochrony jest ekranowanie podzespołów na płytkach PCB, ekranowanie otworów wentylacyjnych przy użyciu tzw. plastrów miodu i ekranowanie okien szczególnie przydatne przy produkcji wszelkiego typu wyświetlaczy, tabletów i komputerów przemysłowych.
ETAP III – interfejs (komunikacja maszyna – człowiek)
Dalsze etapy rozwoju urządzenia związane są z budową interfejsów (przyciski, przełączniki, diody sygnalizacyjne, wyświetlacze) dostosowanych do potrzeb klienta, zastosowaniem materiałów termoprzewodzących oraz ochroną elektromagnetyczną (EMC). Odprowadzanie ciepła jest realizowane przez podkładki o odpowiedniej impedancji cieplnej, które są dopasowywane do kształtów podzespołów, które mają być chłodzone.
ETAP IV – montaż wstępny
DACPOL jako partner w zakresie zabudowy systemów elektroniki oferuje całościowe podejście do problemu projektowania, budowy i ochrony urządzeń elektronicznych. Oferujemy wsparcie w dostawie podzespołów na każdym etapie produkcji, przebudowy i w momencie wdrażania urządzenia na rynek. Co więcej, wspieramy także producentów w zabezpieczaniu urządzeń już gotowych – szczególnie od strony odprowadzania ciepła z płytek PCB i ochrony EMC.
Related products
Related posts
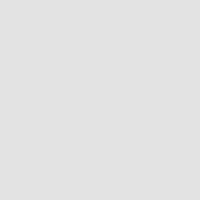
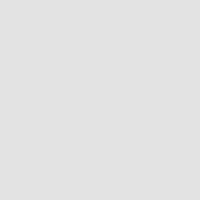
Leave a comment