-
BackX
-
Components
-
-
Category
-
Semiconductors
- Diodes
- Thyristors
-
Electro-insulated Modules
- Electro-insulated Modules | VISHAY (IR)
- Electro-insulated Modules | INFINEON (EUPEC)
- Electro-insulated Modules | Semikron
- Electro-insulated Modules | POWEREX
- Electro-insulated Modules | IXYS
- Electro-insulated Modules | POSEICO
- Electro-insulated Modules | ABB
- Electro-insulated Modules | TECHSEM
- Go to the subcategory
- Bridge Rectifiers
-
Transistors
- Transistors | GeneSiC
- SiC MOSFET Modules | Mitsubishi
- SiC MOSFET Modules | STARPOWER
- Module SiC MOSFET ABB’s
- IGBT Modules | MITSUBISHI
- Transistor Modules | MITSUBISHI
- MOSFET Modules | MITSUBISHI
- Transistor Modules | ABB
- IGBT Modules | POWEREX
- IGBT Modules | INFINEON (EUPEC)
- Silicon Carbide (SiC) semiconductor elements
- Go to the subcategory
- Gate Drivers
- Power Blocks
- Go to the subcategory
- Electrical Transducers
-
Passive components (capacitors, resistors, fuses, filters)
- Resistors
-
Fuses
- Miniature Fuses for electronic circuits - ABC & AGC Series
- Tubular Fast-acting Fuses
- Time-delay Fuse Links with GL/GG & AM characteristics
- Ultrafast Fuse Links
- Fast-acting Fuses (British & American standard)
- Fast-acting Fuses (European standard)
- Traction Fuses
- High-voltage Fuse Links
- Go to the subcategory
- Capacitors
- EMI Filters
- Supercapacitors
- Power surge protection
- TEMPEST emission revealing filters
- Go to the subcategory
-
Relays and Contactors
- Relays and Contactors - Theory
- 3-Phase AC Semiconductor Relays
- DC Semiconductor Relays
- Controllers, Control Systems and Accessories
- Soft Starters and Reversible Relays
- Electromechanical Relays
- Contactors
- Rotary Switches
-
Single-Phase AC Semiconductor Relays
- AC ONE PHASE RELAYS 1 series| D2425 | D2450
- One phase semiconductor AC relays CWA and CWD series
- One phase semiconductor AC relays CMRA and CMRD series
- One phase semiconductor AC relays - PS series
- Double and quadruple semiconductor AC relays - D24 D, TD24 Q, H12D48 D series
- One phase semiconductor relays - gn series
- Ckr series single phase solid state relays
- One phase AC semiconductor relays for DIN bus - ERDA I ERAA series
- 150A AC single phase relays
- Rail Mountable Solid State Relays With Integrated Heat Sink - ENDA, ERDA1 / ERAA1 series
- Go to the subcategory
- Single-Phase AC Semiconductor Relays for PCBs
- Interface Relays
- Go to the subcategory
- Cores and Other Inductive Components
- Heatsinks, Varistors, Thermal Protection
- Fans
- Air Conditioning, Accessories for Electrical Cabinets, Coolers
-
Batteries, Chargers, Buffer Power Supplies and Inverters
- Batteries, Chargers - Theoretical Description
- Modular Li-ion Battery Building Blocks, Custom Batteries, BMS
- Batteries
- Battery Chargers and Accessories
- Uninterruptible Power Supply and Buffer Power Supplies
- Inverters and Photovoltaic Equipments
- Energy storage
- Fuel cells
- Lithium-ion batteries
- Go to the subcategory
-
Automatics
- Spiralift Lifts
- Futaba Drone Parts
- Limit Switches, Microswitches
- Sensors, Transducers
-
Infrared Thermometers (Pyrometers)
- IR-TE Series - Water-proof Palm-sized Radiation Thermometer
- IR-TA Series - Handheld Type Radiation Thermometer
- IR-H Series - Handheld Type Radiation Thermometer
- IR-BA Series - High-speed Compact Radiation Thermometer
- IR-FA Series - Fiber Optic Radiation Thermometer
- IR-BZ Series - Compact Infrared Thermometers
- Go to the subcategory
- Counters, Time Relays, Panel Meters
- Industrial Protection Devices
- Light and Sound Signalling
- Thermographic Camera
- LED Displays
- Control Equipments
- Go to the subcategory
-
Cables, Litz wires, Conduits, Flexible connections
- Wires
- Cable feedthroughs and couplers
- Litz wires
- Cables for extreme applications
- Sleevings
-
Braids
- Flat Braids
- Round Braids
- Very Flexible Flat Braids
- Very Flexible Round Braids
- Cylindrical Cooper Braids
- Cylindrical Cooper Braids and Sleevings
- Flexible Earthing Connections
- Galvanized and Stainless Steel Cylindrical Braids
- PCV Insulated Copper Braids (temp. up to 85C)
- Flat Aluminium Braids
- Junction Set - Braids and Tubes
- Go to the subcategory
- Traction Equipment
- Cable Terminals
- Flexible Insulated Busbars
- Flexible Multilayer Busbars
- Cable Duct Systems
- Go to the subcategory
- View all categories
-
Semiconductors
-
-
- Suppliers
-
Applications
- CNC Machine Tools
- DC and AC Drives (Inverters)
- Energetics
- Energy bank
- Equipment and Components for Hazardous Areas [Ex]
- Equipment for Distribution, Control and Telecommunications Cabinets
- HVAC Automation
- Induction Heating
- Industrial Automation
- Industrial Protective Devices
- Machines for Drying and Wood Processing
- Machines for Thermoforming Plastics
- Mining, Metallurgy and Foundry
- Motors and Transformers
- Power Supplies (UPS) and Rectifier Systems
- Printing
- Temperature Measurement and Regulation
- Test and Laboratory Measurements
- Tram and Railway Traction
- Welding Machines
-
Assembly
-
-
Inductors
-
-
Induction devices
-
-
Service
-
- Contact
- Zobacz wszystkie kategorie
Thermally conductive materials in power storages
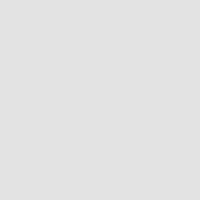
Technological development caused a need in electric engineering to search for new solutions in heat conduction.
The appearance of the thermal-conductive materials on the market made it possible to modernize (mostly miniaturize) application. It became possible due to the thermally conductive abilities of these elements and their electrical insulation. With time, it started to be considered to use them in power banks, which under high temperatures work significantly worse and have more errors.
While designing cooling systems many factors have to be taken into consideration:
- electric resistance (insulation and resistance)
- resistance to external factors (temperature, shocks, dust)
- average and max power of the device
- max working temperature
- cooling system efficiency
- smoothness/porosity of the cooling surface
The most important characterizing parameters of thermally conductive materials are:
Heat conductivity - it is an amount of heat that will flow through a given material in particular conditions and time. Each material has a different value of thermal conductivity, thus not all of them are suitable for heat conduction applications. In thermally conductive materials, mixes of metal oxide particles (filler) are most often used, in various sizes and shapes, to achieve the right value of conductivity.
Thermal resistance - it is a value of resistance which the material offers to the heat flow. In cooling systems, thermal resistance has a huge significance - we want to choose the material with the lowest thermal resistance to achieve the best results in heat conduction. One of the main goals of such applications is to remove air gaps between surfaces of the connectors, because the air has a big thermal resistance.
Types of materials used in battery storage:
Thermally conductive glues - special glues prepared for work in difficult conditions. They are resistant to high temperatures and do not dry, thus can keep their properties for a long time. The usage of the glue increases heat conduction, while connecting the joints, which allows eliminating from the application the need to use screws or clamps. Mostly used for stabilizing and locating the accumulator’s cells, thus decreasing the number of errors while providing an optimal heat conductivity.
Gap fillers (GFL) - are thermal mixes which can be used for encapsulation of the devices and covering the radiators and enclosure’s covers. Their important advantage is the simplicity of application, which allows for protection of complicated geometries. These materials are usually used to create a so-called “conduction track.” This solution increases thermal properties, amortization and application’s stability. Additionally, fillers increase the electrical insulation, which makes the usage of the electric device much safer.
Filling materials - structurally very similar to gap fillers, however, have different mechanical and electrical properties. Filling materials are foils with precise geometry, provided in the shape of sheets or cut out in a special shape of the elements. They are adjusted to compensate for the irregularities of the components, thus most effectively eliminating air bubbles and gaps, and can be used in applications sensitive to pressure.
What are the benefits of using thermally conductive materials?
While analyzing the influence of temperature on the accumulators, it is crucial to notice that variable temperature is a factor that significantly affects the productivity of the battery. The increase of temperature above the recommended one by the suppliers can cause drops in capacity, which can reach up to 50% of the accumulator’s capacity. Work in the wrong temperature can lead to battery aging and increasing its failure frequency. Thus, using materials for effective heat conduction to maintain optimal temperature allows a power storage to work longer and be more efficient.
Thermally conductive materials also allow stabilizing accumulator’s cells towards the vehicle, protecting it from mechanical damages. It is crucial because possible shocks to the power storage can cause active mass of the plates to fall out from cells. This on the other hand leads to the decrease of capacity of the accumulator or, in extreme cases, to internal short circuits. This type of failure damages the accumulator and requires its replacement.
In power storage, errors connected to tidal currents occur. They pose danger to people located in the area. Tidal currents can occur due to: dirty battery block, leakage of the electrolyte through the battery’s enclosure or by occurring cracks and gaps in the battery’s enclosure. Usage of the filler increases electrical insulation, which makes the operation of the system safer and more durable.
Conclusions
Thermally conductive materials can be used in applications producing significant amounts of heat, or in discussed power storage. By using thermally conductive materials we can increase the safety of accumulators and batteries’ exploitation. They provide stabilization of working temperature of such storage, making it possible to be used longer, achieving the highest productivity. In applications at risk of vibrations it is worth considering using fillers to minimize the mechanical damages of accumulators due to the shakes.
After analyzing the benefits of thermally conductive materials in power storage applications it can be stated that they are a cost-efficient investment, which allows to limit the costs connected to the exploitation and service of such devices, providing protection and helping to maintain proper work conditions.
Related products
Related posts
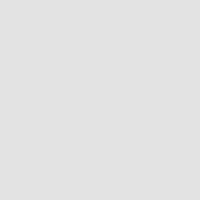
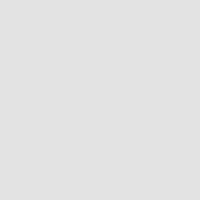
Leave a comment