-
BackX
-
Components
-
-
Category
-
Semiconductors
- Diodes
- Thyristors
-
Electro-insulated Modules
- Electro-insulated Modules | VISHAY (IR)
- Electro-insulated Modules | INFINEON (EUPEC)
- Electro-insulated Modules | Semikron
- Electro-insulated Modules | POWEREX
- Electro-insulated Modules | IXYS
- Electro-insulated Modules | POSEICO
- Electro-insulated Modules | ABB
- Electro-insulated Modules | TECHSEM
- Go to the subcategory
- Bridge Rectifiers
-
Transistors
- Transistors | GeneSiC
- SiC MOSFET Modules | Mitsubishi
- SiC MOSFET Modules | STARPOWER
- Module SiC MOSFET ABB’s
- IGBT Modules | MITSUBISHI
- Transistor Modules | MITSUBISHI
- MOSFET Modules | MITSUBISHI
- Transistor Modules | ABB
- IGBT Modules | POWEREX
- IGBT Modules | INFINEON (EUPEC)
- Silicon Carbide (SiC) semiconductor elements
- Go to the subcategory
- Gate Drivers
- Power Blocks
- Go to the subcategory
- Electrical Transducers
-
Passive components (capacitors, resistors, fuses, filters)
- Resistors
-
Fuses
- Miniature Fuses for electronic circuits - ABC & AGC Series
- Tubular Fast-acting Fuses
- Time-delay Fuse Links with GL/GG & AM characteristics
- Ultrafast Fuse Links
- Fast-acting Fuses (British & American standard)
- Fast-acting Fuses (European standard)
- Traction Fuses
- High-voltage Fuse Links
- Go to the subcategory
- Capacitors
- EMI Filters
- Supercapacitors
- Power surge protection
- TEMPEST emission revealing filters
- Go to the subcategory
-
Relays and Contactors
- Relays and Contactors - Theory
- 3-Phase AC Semiconductor Relays
- DC Semiconductor Relays
- Controllers, Control Systems and Accessories
- Soft Starters and Reversible Relays
- Electromechanical Relays
- Contactors
- Rotary Switches
-
Single-Phase AC Semiconductor Relays
- AC ONE PHASE RELAYS 1 series| D2425 | D2450
- One phase semiconductor AC relays CWA and CWD series
- One phase semiconductor AC relays CMRA and CMRD series
- One phase semiconductor AC relays - PS series
- Double and quadruple semiconductor AC relays - D24 D, TD24 Q, H12D48 D series
- One phase semiconductor relays - gn series
- Ckr series single phase solid state relays
- One phase AC semiconductor relays for DIN bus - ERDA I ERAA series
- 150A AC single phase relays
- Rail Mountable Solid State Relays With Integrated Heat Sink - ENDA, ERDA1 / ERAA1 series
- Go to the subcategory
- Single-Phase AC Semiconductor Relays for PCBs
- Interface Relays
- Go to the subcategory
- Cores and Other Inductive Components
- Heatsinks, Varistors, Thermal Protection
- Fans
- Air Conditioning, Accessories for Electrical Cabinets, Coolers
-
Batteries, Chargers, Buffer Power Supplies and Inverters
- Batteries, Chargers - Theoretical Description
- Modular Li-ion Battery Building Blocks, Custom Batteries, BMS
- Batteries
- Battery Chargers and Accessories
- Uninterruptible Power Supply and Buffer Power Supplies
- Inverters and Photovoltaic Equipments
- Energy storage
- Fuel cells
- Lithium-ion batteries
- Go to the subcategory
-
Automatics
- Spiralift Lifts
- Futaba Drone Parts
- Limit Switches, Microswitches
- Sensors, Transducers
-
Infrared Thermometers (Pyrometers)
- IR-TE Series - Water-proof Palm-sized Radiation Thermometer
- IR-TA Series - Handheld Type Radiation Thermometer
- IR-H Series - Handheld Type Radiation Thermometer
- IR-BA Series - High-speed Compact Radiation Thermometer
- IR-FA Series - Fiber Optic Radiation Thermometer
- IR-BZ Series - Compact Infrared Thermometers
- Go to the subcategory
- Counters, Time Relays, Panel Meters
- Industrial Protection Devices
- Light and Sound Signalling
- Thermographic Camera
- LED Displays
- Control Equipments
- Go to the subcategory
-
Cables, Litz wires, Conduits, Flexible connections
- Wires
- Cable feedthroughs and couplers
- Litz wires
- Cables for extreme applications
- Sleevings
-
Braids
- Flat Braids
- Round Braids
- Very Flexible Flat Braids
- Very Flexible Round Braids
- Cylindrical Cooper Braids
- Cylindrical Cooper Braids and Sleevings
- Flexible Earthing Connections
- Galvanized and Stainless Steel Cylindrical Braids
- PCV Insulated Copper Braids (temp. up to 85C)
- Flat Aluminium Braids
- Junction Set - Braids and Tubes
- Go to the subcategory
- Traction Equipment
- Cable Terminals
- Flexible Insulated Busbars
- Flexible Multilayer Busbars
- Cable Duct Systems
- Go to the subcategory
- View all categories
-
Semiconductors
-
-
- Suppliers
-
Applications
- CNC Machine Tools
- DC and AC Drives (Inverters)
- Energetics
- Energy bank
- Equipment and Components for Hazardous Areas [Ex]
- Equipment for Distribution, Control and Telecommunications Cabinets
- HVAC Automation
- Induction Heating
- Industrial Automation
- Industrial Protective Devices
- Machines for Drying and Wood Processing
- Machines for Thermoforming Plastics
- Mining, Metallurgy and Foundry
- Motors and Transformers
- Power Supplies (UPS) and Rectifier Systems
- Printing
- Temperature Measurement and Regulation
- Test and Laboratory Measurements
- Tram and Railway Traction
- Welding Machines
-
Assembly
-
-
Inductors
-
-
Induction devices
-
-
Service
-
- Contact
- Zobacz wszystkie kategorie
Distance and pressure transducers
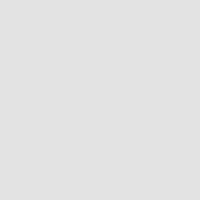
Measuring transducers are used to convert physical quantities into other physical quantities according to specific relationships. Among industrial devices of this type, transducers for electrical values such as voltage or current are the most common. In systems with sensors, transducers allow the power of the transformed signal to be increased in order to facilitate its processing in further industrial processes.
Distance transducers most often convert force or speed into a corresponding output signal in analogue or digital form.
Pressure transducers are used to measure the pressure of gases or liquids, which it converts into a proportional output signal.
In the following article, we will introduce you to the principle of operation and types of specific solutions of distance and pressure transducers.
Working principle of distance and pressure transducers
-
Distance transducer
The working principle of distance transducers is based on sending some kind of signal, e.g. laser, infrared LED, ultrasonic waves or information about the movement and position of the test object by means of a cable attached to it. Then, based on the information about the signal returning to the transducer or the change in position of the test object, an appropriate output signal is generated from the transducer element. This information may include the intensity of the returning signal, the time required for the signal to return, the motion generated on the transducer element, etc. Many devices have additional components that appropriately amplify a given signal so that it can be easily worked on further in industrial processes.
-
Pressure transducer
The most common pressure transducer designs include a force collector, such as a flexible diaphragm, and a conductive element. Such an element uses a dependent resistive, capacitive, or inductive method to generate an electrical signal. The type of measurement method will be determined by the components used to build the transducer.
Pressure transducers use strain gauges to measure the force acting on them. Strain gauges are deformed and this causes a change in the voltage they produce. The pressure measurement is based on the degree of voltage change.
There are also advanced versions of pressure transducers that use capacitive or piezoelectric sensors instead of strain gauges. These are chosen based on the range, operating environment and precision required of the pressure sensor.
Types of transducers available on the market
The type of transducer depends on what signal it is capturing e.g. distance using reflected light and motion using a cable in the case of distance transducers , or the type of pressure being measured in the case of pressure transducers. An additional factor influencing the type may also be the output signal of the transducer e.g. current voltage, current intensity or digital value. Depending on these factors, the transducer may differ in its internal design.
Examples of distance transducers
There are many unique options to choose from for distance transducers. We focus primarily on three varieties of distance sensors:
- IR LED distance transducers work on the principle of triangulation, measuring distance based on the angle of the reflected beam. The beam of infrared light emitted by the LED is reflected from the object under observation at a certain angle. The reflected beam is read by a transducer detector to process the collected data into a specific output signal.
Such solutions are characterized by their small size, ability to work at any time of day or night, and ability to measure distances from objects with complex surfaces. The disadvantages of such applications, however, are a limited measuring range and dependence on environmental conditions and, for example, the colour of the measuring object.
- Ultrasonic distance transducers detect the distance to objects by emitting high frequency sound waves. The emitter sends the wave toward the object and activates a timer. The wave bounces off the object and is captured by the transducer's receiver, then the timer is stopped. The distance is calculated from the speed of sound and the travel time of the high frequency wave.
The advantages are transparency and the ability to work with objects of any color. The solution does not consume as much power as other applications, but also has a limited measurement range, low resolution, inability to measure objects with uneven surfaces as well as objects that move at high speed.
- Link Distance Transducers measure position using a string that coils and unwinds on a measuring spool. The end of the string is attached to the test object, and its motion affects the spool. A rotary reader (potentiometer or encoder) transmits the rotational motion of the spool to the appropriate components, which convert it into an output signal.
Examples of pressure transducers
For pressure transducers, there are three defined values for measuring pressure. Although there are other types, such as vacuum or sealed gauge, all can be classified into these three categories. For the diaphragm type, it is easiest to understand the reference pressure as the pressure exerted across the diaphragm from the process being measured.
- Absolute pressure transducers measure pressure relative to an ideal vacuum using absolute zero as a reference. An example is a barometric pressure transducer. They also include sealed pressure gauges in which the signal has been shifted to match the pressure of the gauge at the time of construction.
- Gauge pressure transducers measure pressure relative to atmospheric pressure. An example of such a sensor is a tire pressure sensor. It also includes vacuum sensors whose signals are inverted so that they signal a positive result when the measured pressure is lower than atmospheric pressure.
- Differential pressure transducers measure the difference between two pressures on each side of the sensor. An example is a fluid pressure transducer, in which the level of the fluid above and below is measured.
Applications for transducers in industry
Distance transducer applications:
- Automation and Robotics;
- Smart cars;
- Drones and unmanned vehicles;
- TVs, computers;
- Security systems such as alarms;
- Systems for industrial process control and monitoring.
Pressure transducer applications:
- Pressurized Engine Systems;
- Production and assembly lines;
- Containers with production material;
- Sanitary systems in the pharmaceutical industry;
- Control systems, e.g. gas leakage detection;
- HVAC systems.
Related products
Related posts
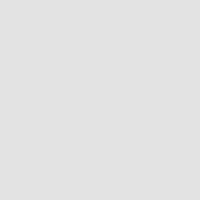
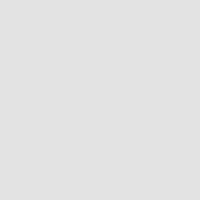
Leave a comment