-
BackX
-
Components
-
-
Category
-
Semiconductors
- Diodes
- Thyristors
-
Electro-insulated Modules
- Electro-insulated Modules | VISHAY (IR)
- Electro-insulated Modules | INFINEON (EUPEC)
- Electro-insulated Modules | Semikron
- Electro-insulated Modules | POWEREX
- Electro-insulated Modules | IXYS
- Electro-insulated Modules | POSEICO
- Electro-insulated Modules | ABB
- Electro-insulated Modules | TECHSEM
- Go to the subcategory
- Bridge Rectifiers
-
Transistors
- Transistors | GeneSiC
- SiC MOSFET Modules | Mitsubishi
- SiC MOSFET Modules | STARPOWER
- Module SiC MOSFET ABB’s
- IGBT Modules | MITSUBISHI
- Transistor Modules | MITSUBISHI
- MOSFET Modules | MITSUBISHI
- Transistor Modules | ABB
- IGBT Modules | POWEREX
- IGBT Modules | INFINEON (EUPEC)
- Silicon Carbide (SiC) semiconductor elements
- Go to the subcategory
- Gate Drivers
- Power Blocks
- Go to the subcategory
- Electrical Transducers
-
Passive components (capacitors, resistors, fuses, filters)
- Resistors
-
Fuses
- Miniature Fuses for electronic circuits - ABC & AGC Series
- Tubular Fast-acting Fuses
- Time-delay Fuse Links with GL/GG & AM characteristics
- Ultrafast Fuse Links
- Fast-acting Fuses (British & American standard)
- Fast-acting Fuses (European standard)
- Traction Fuses
- High-voltage Fuse Links
- Go to the subcategory
- Capacitors
- EMI Filters
- Supercapacitors
- Power surge protection
- TEMPEST emission revealing filters
- Go to the subcategory
-
Relays and Contactors
- Relays and Contactors - Theory
- 3-Phase AC Semiconductor Relays
- DC Semiconductor Relays
- Controllers, Control Systems and Accessories
- Soft Starters and Reversible Relays
- Electromechanical Relays
- Contactors
- Rotary Switches
-
Single-Phase AC Semiconductor Relays
- AC ONE PHASE RELAYS 1 series| D2425 | D2450
- One phase semiconductor AC relays CWA and CWD series
- One phase semiconductor AC relays CMRA and CMRD series
- One phase semiconductor AC relays - PS series
- Double and quadruple semiconductor AC relays - D24 D, TD24 Q, H12D48 D series
- One phase semiconductor relays - gn series
- Ckr series single phase solid state relays
- One phase AC semiconductor relays for DIN bus - ERDA I ERAA series
- 150A AC single phase relays
- Rail Mountable Solid State Relays With Integrated Heat Sink - ENDA, ERDA1 / ERAA1 series
- Go to the subcategory
- Single-Phase AC Semiconductor Relays for PCBs
- Interface Relays
- Go to the subcategory
- Cores and Other Inductive Components
- Heatsinks, Varistors, Thermal Protection
- Fans
- Air Conditioning, Accessories for Electrical Cabinets, Coolers
-
Batteries, Chargers, Buffer Power Supplies and Inverters
- Batteries, Chargers - Theoretical Description
- Modular Li-ion Battery Building Blocks, Custom Batteries, BMS
- Batteries
- Battery Chargers and Accessories
- Uninterruptible Power Supply and Buffer Power Supplies
- Inverters and Photovoltaic Equipments
- Energy storage
- Fuel cells
- Lithium-ion batteries
- Go to the subcategory
-
Automatics
- Spiralift Lifts
- Futaba Drone Parts
- Limit Switches, Microswitches
- Sensors, Transducers
-
Infrared Thermometers (Pyrometers)
- IR-TE Series - Water-proof Palm-sized Radiation Thermometer
- IR-TA Series - Handheld Type Radiation Thermometer
- IR-H Series - Handheld Type Radiation Thermometer
- IR-BA Series - High-speed Compact Radiation Thermometer
- IR-FA Series - Fiber Optic Radiation Thermometer
- IR-BZ Series - Compact Infrared Thermometers
- Go to the subcategory
- Counters, Time Relays, Panel Meters
- Industrial Protection Devices
- Light and Sound Signalling
- Thermographic Camera
- LED Displays
- Control Equipments
- Go to the subcategory
-
Cables, Litz wires, Conduits, Flexible connections
- Wires
- Cable feedthroughs and couplers
- Litz wires
- Cables for extreme applications
- Sleevings
-
Braids
- Flat Braids
- Round Braids
- Very Flexible Flat Braids
- Very Flexible Round Braids
- Cylindrical Cooper Braids
- Cylindrical Cooper Braids and Sleevings
- Flexible Earthing Connections
- Galvanized and Stainless Steel Cylindrical Braids
- PCV Insulated Copper Braids (temp. up to 85C)
- Flat Aluminium Braids
- Junction Set - Braids and Tubes
- Go to the subcategory
- Traction Equipment
- Cable Terminals
- Flexible Insulated Busbars
- Flexible Multilayer Busbars
- Cable Duct Systems
- Go to the subcategory
- View all categories
-
Semiconductors
-
-
- Suppliers
-
Applications
- CNC Machine Tools
- DC and AC Drives (Inverters)
- Energetics
- Energy bank
- Equipment and Components for Hazardous Areas [Ex]
- Equipment for Distribution, Control and Telecommunications Cabinets
- HVAC Automation
- Induction Heating
- Industrial Automation
- Industrial Protective Devices
- Machines for Drying and Wood Processing
- Machines for Thermoforming Plastics
- Mining, Metallurgy and Foundry
- Motors and Transformers
- Power Supplies (UPS) and Rectifier Systems
- Printing
- Temperature Measurement and Regulation
- Test and Laboratory Measurements
- Tram and Railway Traction
- Welding Machines
-
Assembly
-
-
Inductors
-
-
Induction devices
-
-
Service
-
- Contact
- Zobacz wszystkie kategorie
Hydrogen Fuel Cells - Key Information
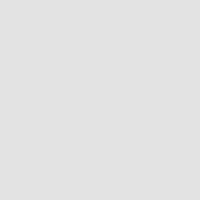
The technological development and changes in the global industry force the continuous need to search for new energy sources. When it comes to batteries, the focus is not only on high efficiency, capacity, or performance but also on ecology and the ability to operate in various conditions. Therefore, the problem boils down to balancing many factors, and the solutions proposed by manufacturers focus on delivering specialized devices to the market. The electrolyte or the use of substances with properties and parameters that will influence the effectiveness of energy sources is also essential.
A breakthrough in this field has been fuel cells, which, as electrochemical devices, allow the generation of electrical energy and heat from the reactions occurring within them. In short: in fuel cells, the conversion of chemical energy from fuels such as hydrogen, methane, butane, methanol, or gasoline into electrical energy takes place.
DACPOL, addressing these needs and responding to market expectations, has introduced hydrogen-based solutions into its offer, which will be expanded in the future to include other energy sources. Currently, we offer PEM fuel cells of various power ratings, as well as complete power systems containing a ventilation system, converter, and housing.
Hydrogen - The simplest and lightest element
It is the simplest (composed of one proton and one electron) and lightest (14 times lighter than air) chemical element that starts the periodic table and accounts for about three-fourths of the mass of the Universe. Hydrogen is contained in water covering about 70% of the Earth's surface, as well as in all organic matter. Under normal conditions, hydrogen is a colorless, tasteless, and odorless gas, slightly soluble in water (0.021 vol. H2 in 1 vol. H2O at 0°C). The low critical temperature of hydrogen (-239.9°C) makes its liquefaction more difficult than that of air and most other gases. Liquefied hydrogen is a colorless liquid with a specific gravity of 0.07 g/cm3. Due to its small molecular mass (2.0158), hydrogen gas exhibits the lowest specific gravity among all gases - 0.08988 g/l at 0°C and 1 atm. Compared to other gases, it also has a high diffusion speed and is the best thermal conductor among them. It is a flammable gas, burning with a clean, carbon- and soot-free flame. In comparison with other popular fuels like gasoline, methane, and propane, hydrogen has a clearly higher calorific value, heat of combustion, ignition energy, and flame speed.
Hydrogen storage
High shares of renewable energy sources in the power system can require long-term and seasonal storage, for example, to provide electricity for several days during periods of very low wind and sunlight.
Hydrogen and hydrogen fuels, such as methane, liquid organic hydrogen carriers (LOHCs), and ammonia produced by electricity through electrolysis, are potential options for long-term and large-scale energy storage. Salt caverns are the best choice for underground storage of pure hydrogen due to their tightness and low risk of contamination. Alternative underground hydrogen storage options are also being explored, such as caves, aquifers, and places left after oil and gas extraction.
Converting electrical energy into methane using energy produced from natural gas is another option for long-term hydrogen storage.
Pure hydrogen is mostly stored in pressure vessels. Few construction materials are used for manufacturing hydrogen storage tanks, as hydrogen significantly increases their brittleness. The best current solution is ultralight composite materials that withstand pressures above 20 bar. These materials are used in prototypes of cars and buses.
Among them, the following should be mentioned:
- Metal tanks made of steel, capable of withstanding 200 bar, or aluminum tanks, capable of withstanding a maximum pressure of 175 bar.
- Aluminum tanks reinforced with fiberglass, aramid, or carbon fibers, capable of withstanding maximum pressures above 250 bar.
- Bottles made of fiberglass/aramid composites or carbon fiber with a metal liner, capable of withstanding maximum pressures of 305 and 438 bar, respectively.
- Bottles made of typical carbon fiber coated with a polymer layer, capable of withstanding pressures above 661 bar.
Carbon Nanofibers - A material of the future for hydrogen storage tanks
Carbon nanofibers, including carbon nanotubes, are the material of the future for manufacturing hydrogen storage tanks. These structures have exceptional electrical and mechanical properties, resembling, under electron microscopy, a mat made from intertwined carbon threads. They conduct heat well and exhibit high strength, making them one of the strongest and stiffest materials discovered to date.
Some tanks are used for long-term hydrogen storage, while others are designed for continuous filling and emptying.
Hydrogen is also stored in liquid form. Liquid hydrogen tanks can be used in transport and portable devices. However, the technology for producing liquid hydrogen requires significant energy input, as it must be cooled to a very low temperature (-252.87°C) once compressed.
The main advantage of storing hydrogen in liquid form, rather than gas, is that it occupies a much smaller volume.
Liquefied hydrogen has found use as rocket fuel in internal combustion engines and fuel cells. During the combustion of hydrogen in a rocket engine, large amounts of energy are generated, releasing water along with trace amounts of ozone and hydrogen peroxide.
Typical hydrogen applications
- Mixtures of argon with hydrogen are used as shielding gases in plasma welding and TIG welding. These mixtures are primarily used when welding austenitic stainless steel and some nickel alloys.
- Hydrogen, combined with argon, can also be used to produce mixtures for plasma cutting (mainly for stainless steel and aluminum). In glass manufacturing, hydrogen is used to polish edges.
- Hydrogen is also used in the production of carbon steels, special metals, and semiconductors.
- In electronics, hydrogen is commonly used as a reducing agent and carrier gas.
- Other processes involving hydrogen include hydrofining of petroleum products, desulfurization of exhaust gases, heat treatment of metals, and leak testing. Hydrogen is also used in various petrochemical and chemical processes.
- Hydrogen is used to power flames in industrial and laboratory burners.
PEM Fuel Cells - How Do Hydrogen Fuel Cells Work?
The PEM (Proton Exchange Membrane or Polymer Electrolyte Membrane) technology involves supplying fuel cells with pure hydrogen or reformate. The membrane in this case is a polymer material such as Nafion. A characteristic feature of PEM fuel cells is their high efficiency in generating electricity – up to 65% – and the low amount of heat generated. Another advantage is the good responsiveness of the cell in systems subjected to varying loads, as well as the short startup time. These properties result from the low reaction temperature within the fuel cell: 60 – 100°C.
The electrolyte allows the flow of cations while preventing the flow of electrons. The chemical reaction within the fuel cell involves splitting hydrogen into protons and electrons at the anode, followed by combining the reaction substrates at the cathode. Electrochemical processes are accompanied by the flow of electrons from the anode to the cathode, bypassing the impermeable membrane. As a result of the electrochemical reaction between hydrogen and oxygen, electric current, water, and heat are produced. The fuel – hydrogen in its pure form or mixed with other gases – is continuously supplied to the anode, and the oxidizer – oxygen in its pure form or a mixture (air) – is continuously supplied to the cathode.
Fuel cells theoretically do not discharge. In practice, degradation or malfunction of components limits their lifespan. The main applications of PEM fuel cells are vehicle propulsion and the construction of stationary or portable power generators.
Advantages of Hydrogen Fuel Cells
High reliability – no moving parts, high quality of the energy supplied. The energy delivered by fuel cells is highly resistant to interference.
Hydrogen fuel cells are an ideal power source for medical devices, measuring equipment, computers, etc. Fuel cells are characterized by high efficiency and energy density.
A fuel cell is always smaller and lighter than other energy sources with comparable power.
Fuel cell efficiency in generating electricity can reach up to 50%. In the process of cogeneration, producing both electricity and heat, fuel cells achieve an efficiency of up to 85%. Various types of fuels can be used in fuel cells.
Fuel cells can be powered by any fuel rich in hydrogen. Hydrogen can be obtained from fuel either inside the fuel cell, through internal reforming, or outside the cell using an external device called a fuel reformer.
Thanks to electrolysis, hydrogen for fuel cells can be produced using alternative energy sources. Pollution resulting from the production of energy using "conventional" methods is a cause of environmental degradation and the emergence of new civilization diseases. A fuel cell produces 25 times fewer pollutants compared to internal combustion generators.
When the fuel cell is powered by hydrogen, the amount of pollutants produced is minimal. Individual fuel cells can be combined to achieve the desired power generation level (scalability). Fuel cell assemblies of different shapes are used to power everything from a single light bulb to industrial machinery. PEM fuel cell applications also include vehicle propulsion and the construction of stationary or portable power generators.
The principle of operation of the hydrogen fuel cell is well known, and progress is currently being made in the development of materials for electrodes, membranes, seals, and catalysts. The goal of research is to extend the lifespan and efficiency of the cell while reducing production costs. Additionally, new technologies for manufacturing fuel cell components are being developed by replacing mechanical processing with precise spray technologies. The effects of this research are already visible to end-users: the lifespan of fuel cells is increasing, and the cost of produced energy is decreasing.
DACPOL's offer includes not only the delivery of fuel cells themselves but also complete systems and support for working with hydrogen technology.
The simplest form of cooperation is the design and construction of a hydrogen fuel cell tailored to the user's individual needs. The requirements may concern not only electrical parameters but also environmental conditions, working conditions, application, or special construction. The production phase is actually the final stage of the entire process, which begins with a thorough understanding of the customer's needs and the establishment of subsequent design steps.
Key characteristics of fuel cells supplied by DACPOL are:
- High energy density, related to the appropriately designed microstructure of the elements comprising the stack,
- Simplified construction making the stack more compact, lighter, and more efficient than similar solutions,
- Scalability enabling the construction of larger solutions (with higher power).
In addition to supplying hydrogen fuel cells as energy sources, DACPOL also offers the possibility of building a complete hydrogen-based power system for the customer. This solution includes the fuel cell, heat exchanger, inverter, and housing for mechanical protection along with assembly. We will also assist in selecting appropriate components if the user already has some of the elements of the above system.
Related products
Related posts
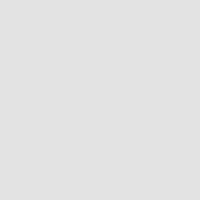
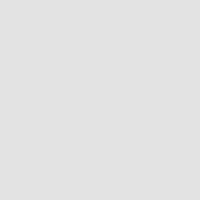
Leave a comment
Comments
Pytanie o cenę ogniwa paliwowego o mocy 5.5kW , 12 kW oraz 25kW
By: Tomasz On 15-11-2024Dobieram ogniwo paliwowe do instalacji wodorowej dla zasilania obiektu w zimę. Pozdrawiam,
Replied by: Michał DACPOL On 15-11-2024